Subscribe to NDT Trends
Change Password
Preferences
I, hereby state that I would like to subscribe to the following related content
Are you sure you want Sign out?
NEWSLETTER
Get the latest insights from the NDT world delivered straight to your inbox
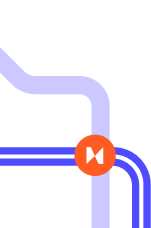
Hello, Friend!
Enter your personal details and start journey with us
By continuing, you agree to OnestopNDT's
Terms of
Service
and
acknowledge that you've read our Privacy Policy
or
Continue with Google
By continuing, you agree to OnestopNDT's
Terms of
Service
and
acknowledge that you've read our Privacy Policy
Hey, there !
Enter your personal details and start your NDT journey with us
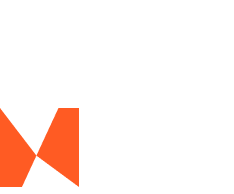
Widen your organization’s reach and services
Get an exclusive opportunity to promote your services, events and webinars
Be a part of a platform with like-minded NDT professionals
Be a part of a platform with like-minded NDT professionals
Thank you so much! The June edition was really excellent. It provided a detailed information on offshore & Titan topic that were very trending in our circles. Great work!
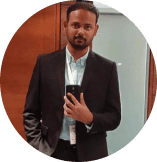
Anoop Rayavarapu
NDT Manager | NDT Consultant | QA/QC Lead | Business Dev. Manager | Executive Manager |
NDT Trends has become my favorite magazine for exploring the fascinating world of non-destructive testing. The blend of technical expertise and real-world applications is impressive.
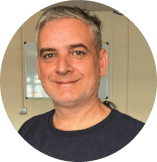
Paul Bentley
Director at Lizard NDE Ltd
I found the July edition of NDT Trends really amazing especially the article on Titan Submersible was very engrossing and very informative. Really looking forward to the future editions.
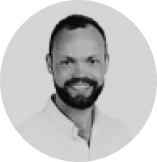
Niels Delore
Managing Director for Asia Pacific at Flyability
I appreciate how NDT Trends bridges the gap between research and application. It's an honor to be one of contributors in NDT Trends magazine's latest edition.
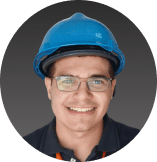
Ahmed Reda
Fresh Graduate Refining & Petrochemical Engineer | Aspen Certified User in Aspen HYSYS®
Having been in the NDT industry for decades, I can confidently say that NDT Trends stands out as a premier publication. It’s commitment to quality content and staying ahead of industry trends makes it a reliable source for NDT professionals.
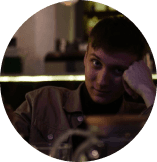
Anton Nosyrev
Sales manager at TWN Technology

UT Across Borders:
How Standards, Expectations,
and Certifications
Vary Around
the World
Aug 2025
Moderator

Eddie Pompa
Panelists

Paul Holloway

George Shields

Sandeep Murjani

Justin Cavanagh