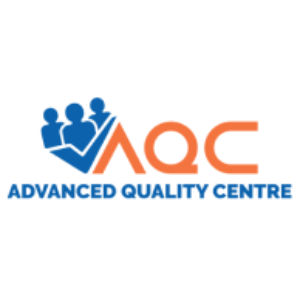
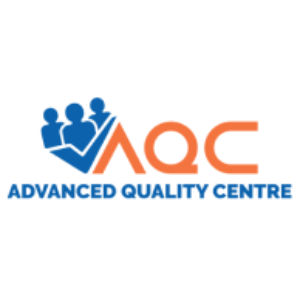
Advanced Quality Centre
AQC will be the most trusted industrial training, inspection & testing service provider and consistently will grow global. We aim to produce the most competent engineers through our training methods.


Overview
Advanced Quality Centre is an ISO 9001:2015 certified center; we provide world-class training & certifications for Non-Destructive Testing, Welding Inspections, Painting Inspections, safety training & Industrial testing services; the training is provided by engineers experienced in global industries for more than a decade,
We are teamed with experienced engineers to make quality audits & provide ISO Certifications,
We provide mechanical testing services such as Chemical Analysis, Tensile, Micro, Macro, Impact & hardness tests.
We do third painting inspections and train company employees to do painting inspections.
Highlights
- World-class training facilities & quite an ambiance classrooms.
- Students are trained by the most experienced industry experts, worked in countries
- ISO Certified Company
- 100% job guidance for a lifetime
- Our team is guided by Metallurgists mastered from IIT, Mumbai & Delhi.
- Our safety officers have experienced different projects such as metro rail, Oil, Gas Extraction & refineries.
QUALITY POLICY
AQC Pledged to
- Provide timely, reliable, cost-efficient & quality testing, inspection & training services.
- To fulfill all the requirements of the referencing quality standards
- Deliver 100 % technical data & assure competency in trainees during training
Products
Services
Ads
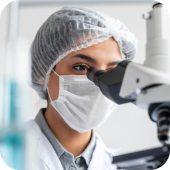
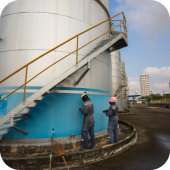
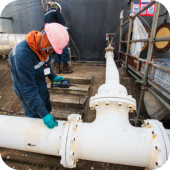