Eddy Current NDT
Spot-Weld Ultrasonic Inspection
Published on 10th December 2020
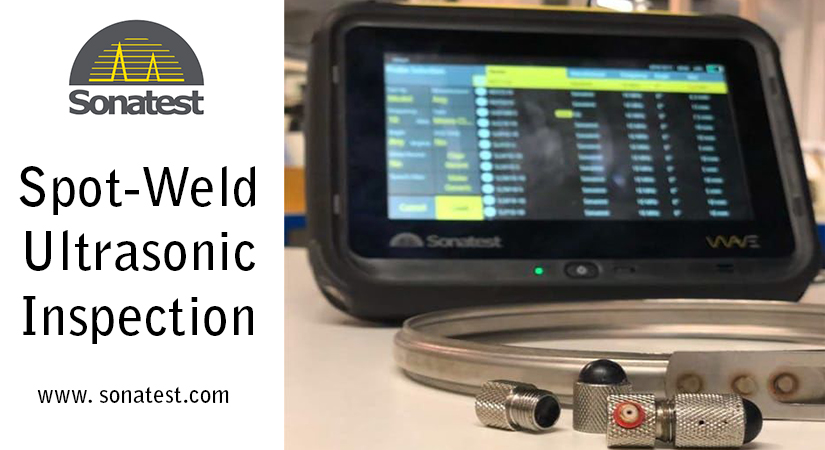
Brief Description
Spot-welds on automotive components and other structures require inspection for a number of possible failure modes including adhesive (stick) welds, burnt welds and non-fused welds.
Sonatest rubber tips are designed to be used with the RDT delay line family and offer an effective alternative to the more traditional approach of water filled contact probes. They have better life expectancy than water filled tips and the use of rubber dramatically reduces the amount of couplant required to ensure good contact. The flexible surface works exceptionally well on uneven surfaces
Using the pulse echo technique, the following results may be seen:
1. Good weld
With a good spot weld, the amplitudes of the subsequent echoes drop relatively quickly because the weld structure is coarse grained and therefore has a high sound attenuation characteristic. The echo intervals correspond to the total thickness of the welded sheets.
2. Adhesive / Loose / Stick weld
If there is an adhesive weld (also called a cold shot or a stick weld), then an extended echo sequence is received from the two sheets. In the case of a cold shot, however the grain structure is different (fine grained) and this leads to a long echo sequence due to reduced sound attenuation.
3. Burnt weld
If a burnt weld condition is present then the weld material is highly attenuative due to the coarser grain structure is possesses. This leads to the transmitted ultrasound dropping off rapidly because of the higher attenuation, as shown above with the reduction in echoes received and amplitude.
4. Non-fused / Loose plate
A non-fused/loose weld leads to a long echo sequence with short echo intervals corresponding to the single (upper) plate thickness only.
Conclusion
Manual testing can be very effective in detecting ‘defective’ weld conditions associated with spot weld joining process. This is always operator dependant and needs a good basic understanding of ultrasonic principles. The main benefit of manual testing is primarily the low cost and portability when compared to larger fixed or robotic systems.
Industries
- Automotive
- Manufacturing
- Aerospace
- Construction
- Rail
Typical Parts
- Chassis
- Rails
- Tools
- Sheet Metals
- Wire Mesh (Welded Mesh)
- Batteries
Features & Benefits
- Easy to set up
- Simple executive procedure
- Fast & reliable inspection
- Cost efficient
Recommended Package
- WAVE or D70
- RB2010 10 MHz probe
- 10 mm spot-weld ball
- 151631 and 151635
For further information or support, please contact the Sonatest Applications Team: applications@sonatest.com
Source: https://sonatest.com/resources/application-notes/spot-weld-ultrasonic-inspection