Ultrasonic NDT
Measuring Coating Thickness on Composite Aircraft: From Total Thickness to Individual Layers
Published on 30th January 2023
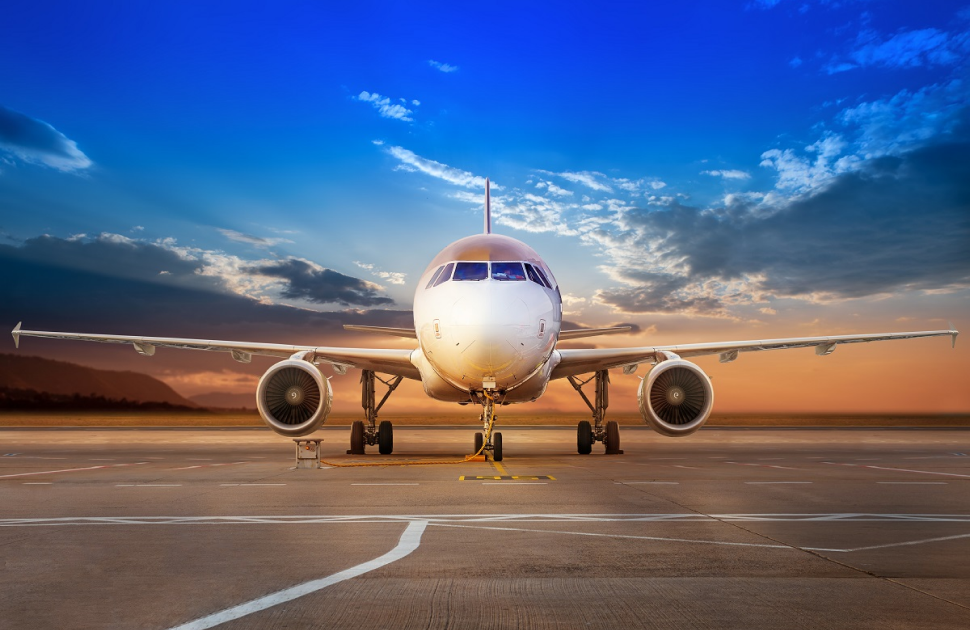
This application note explains how to measure the total thickness and individual layer thickness in multilayer coatings on aerospace composite. Controlling the thickness of paint and coatings on composite aircraft is important in the initial production and after damaged areas have been repaired and repainted.
Background on Composite Materials Used in Aircraft
The biggest advantage of using composite in the production of aircraft is weight reduction. Composite materials enable manufacturers to shed excess weight from planes, making the planes more aerodynamically efficient. The more composite material used in the aircraft, the more efficient an aircraft can be.
Coatings on composites provide several important functions in addition to adding decorative appeal and showing an airline’s branding. One of the most important technical reasons to paint aircraft composites is to protect the composite from fluid damage. Some resins are affected by long-term contact with water, and changes in atmospheric condition, such as freezing and thawing, can cause damage to the composite structures. Coatings can also protect composites from other damage caused by fluids such as hydraulic fluid, fuel, and deicer. Aircraft composite coatings need to be lightweight, flexible, resistant to fluids and corrosion, and provide long-term durability for a long service life.
The Importance of Measuring Coating Thickness on Composite Aircraft
Controlling the coating thickness helps to reduce the weight of the aircraft. If the coating becomes too thick, it can also affect the efficiency of the lighting strike protection of the aircraft. Aircraft composites often use a type of metal foil mesh, such as a thin layer on top of the composite or metal wires that are woven or embedded in the top layer of the composite. This mesh is typically added to the areas on an aircraft that are susceptible to lighting strikes. The metal mesh enables the composite material to dissipate a lightning strike over the surface of the aircraft in the same way it would in an aluminum body aircraft.
The total thickness of the paint or coating on a composite aircraft is typically the most important factor for quality control. Knowing the individual thickness of each layer of a coating is also important for quality control in many cases, as it can help control the consistency of each layer as it is being applied. The coating on a composite aircraft generally has four or more layers, including an anti-static coating, surfacer layer, primer, and more than one topcoat.
Ultrasonic Equipment Used to Measure Coating Thickness on Composite Aircraft
Some advanced ultrasonic thickness gauges can measure the total thickness of a coating and its individual layers with one test. This functionality gives aircraft manufacturers the capability to confirm total thickness and individual layer thickness with greater efficiency.
The total thickness of the coatings on composite aircraft is typically under about 0.020 in. (0.50 mm), while individual layers can be as thin as 0.002 in. (0.050 mm). The 72DL PLUS™ ultrasonic thickness gauge works with single-element transducers in a broad frequency range of 0.5 MHz to 125 MHz, enabling the measurement of very thin coatings and layers. Most precision ultrasonic thickness gauges can only use transducers up to about 20 MHz, limiting their ability to measure thin coatings.
The 72DL PLUS gauge can also measure and display up to 6 individual layer thicknesses at once. As manufacturing processes can vary, it is important to evaluate your specific application to determine if total thickness or individual layer thickness is achievable.
Procedure to Measure the Coating Thickness on Composite Aircraft
The following example shows the thickness measurement of a multilayer coating on aerospace composite using ultrasonic gauging equipment.
Total thickness: This measurement uses a transducer in the 20–50 MHz range. The thickness gauge is adjusted to suppress echoes from the internal layers. The gauge takes a total thickness measurement from the front surface to the top of the composite structure.
The waveform below shows the signal from an aircraft composite with a surfacer layer and two topcoats. The display is optimized to measure the total thickness of the three layers on the aircraft composite sample. The measurement was taken on the 72DL PLUS gauge using the M2017 (20 MHz) transducer.
Individual layer thickness: In this measurement, the 20 MHz transducer and ultrasonic setup are optimized to amplify the echoes for each of the three layers of the coating on the composite. The coating includes a surfacer layer and two topcoat layers.
The waveform below displays the three individual layers and the total thickness (summation) of all the layers on a composite aircraft sample. The measurement was taken on the 72DL PLUS gauge with a M2017 (20 MHz) transducer.
Products used for this application
The 72DL PLUS™ advanced ultrasonic thickness gauge delivers precision thickness measurements at high speed in a portable, easy-to-use device. Compatible with single element transducers up to 125 MHz, this innovative instrument is ideally suited to measure the thickness of ultra-thin materials, including multilayer paint, coatings, and plastic. It can simultaneously display the thickness of up to 6 layers.
The 38DL PLUS is an advanced ultrasonic thickness gauge. Uses dual element transducer for internal corrosion applications, and has features that include THRU-COAT technology and echo-to-echo. Uses single element transducers for very precise thickness measurements of thin, very thick, or multilayer materials.
Source: https://www.olympus-ims.com/en/applications/measuring-coating-thickness-on-composite-aircraft/