Magnetic Flux Leakage Testing
Assessing Buried Aviation Fuel Tanks for Fitness For Purpose
Published on 23rd November 2020
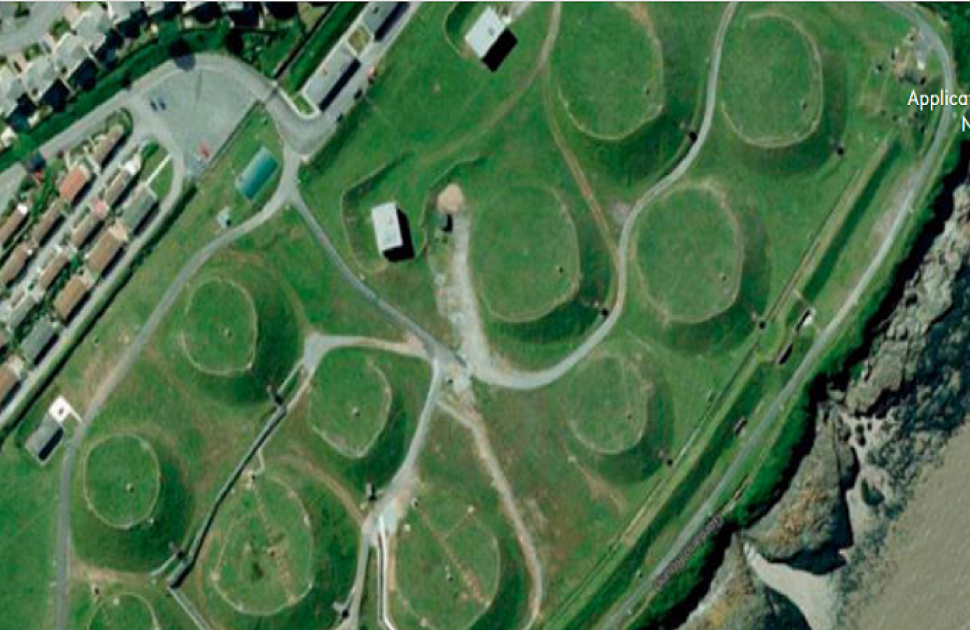
Source: Assessing Buried Aviation Fuel Tanks for Fitness For Purpose (eddyfi.com)
In 1941, during the second world war, an aviation fuel storage tank was built to store Avgas, or aviation fuel, to supply the US Air Force. The design of the tank is typical of a British wartime storage tank. Earth was mounded over and around the tank and grass grew providing camouflage from enemy aircraft. The roof of the storage tank was reinforced with a concrete lining. Taken out of military service during the early 1950s, the buried tank was reinstated for commercial use in 1953. The tank has remained in commercial use since 1953 and has been used to hold aviation fuel reserves for one of the world’s busiest airports.
The Challenge
Determine condition of large, semi-buried aviation fuel storage tank located in southern England
Semi-buried bulk fuel storage tanks
Regular fuel sampling indicated an increase in water content over the years, and the tank owner/operator had concerns about the integrity of the tank’s roof and internal roof lining. No formal inspection records were currently available for the tank; its condition was unknown. An internal survey of the tank was required to determine its current condition and determine its fitness for purpose. The owner would need to take the tank offline, evaluate the inspection results, make any repairs required, and return the tank to service within a very tight timeline.
The Solution
Magnetic flux leakage, ultrasonic testing, visual and magnetic particle inspection for comprehensive assessment of entire tank
Underside of floor cutouts showing underfloor corrosion
Characteristic circular staining around weld highlights pinhole type leak
With access provided to the cleaned tank, inspection was performed utilizing advanced Silverwing instruments. Visually, the floor plates appeared to be in excellent condition considering the age of the tank. However, a Magnetic Flux Leakage (MFL) survey identified multiple areas of tank floor that had been attacked by underfloor corrosion. The most severe corrosion was recorded at 75 percent loss of the nominal plate thickness. Several coupons were selected to be cut from the floor, and physical measurements verified the accuracy of the MFL results. Despite the severity of corrosion, results showed that most of the corroded regions were limited to isolated or localized areas, so the tank was deemed repairable.
Ultrasonic Testing (UT) was employed to survey the tank shell with no significant thinning detected. A leak was noted on a shell plate weld during this inspection. Although the perforation in the weld was extremely small, it was easily identified by a characteristic circular damp area caused by leaked product being drawn back into the tank due to capillary action. This was remedied using a “chemical metal” compound.
Visual inspection of the roof lining did not reveal any suspect areas; however, a continuously damp area on a floor plate led to the detection of a roof leak. The area was excavated and repaired externally.
Inspection results showed that except for the floor plates, the tank was in relatively good condition considering its age.
Benefits
- Complementary technologies offer confidence in data to take corrective actions and have auditable record
The tank owner was able to leverage the reporting software to make several cost calculations based on different repair scenarios by using the corrosion display filters. The software was set to display defects more than 40, 50 or 60 percent loss. At each display threshold, the owner calculated the time, material, and labour costs required to repair the corroded areas, able to make informed decisions based on repair costs versus expected service life.
Due to the semi-buried nature of this tank, the owner was able to take more cost-effective measures than replacement offered. All corrosion more than 60% loss was repaired, and a five-year internal inspection regime was introduced for all tanks onsite.
A comparison of results later showed that the underfloor corrosion had not grown significantly between inspection. The tank owner was able to use software reporting tools for tank comparison and patch plate design to make calculations within a matter of hours rather than a matter of days as was the case during the initial inspection.