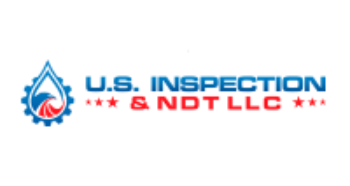
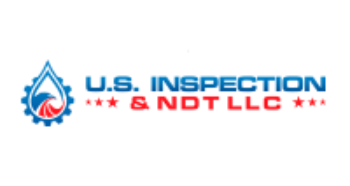
U.S. Inspection & NDT, LLC
U.S. Inspection & NDT, LLC began operations in 2019 in collaboration with William "Billy" Schneider and David Chamberlain to serve a wide array of clients who shared one common goal.


Overview
U.S. Inspection & NDT, LLC began operations in 2019 in collaboration with William "Billy" Schneider and David Chamberlain to serve a wide array of clients who shared one common goal - to partner with testing professionals who provide reliable results and never lose sight of customer goals and service.
U.S. Inspection & NDT, LLC applies a spectrum of technologies for non-destructive testing. We cost-effectively offer industry-standard methodologies and adopt new technologies as they emerge. When innovation is combined with customer collaboration, USINDT can present solutions that meet the scope of every project on time and under budget.
Our clients depend on USINDT to not only identify discontinuities but also to advise them on the proper techniques of non-destructive testing needed for their materials or equipment. This is where USINDT’s competitive advantage comes into play in the knowledge and experience of our people.
Our industry is based on client relationships. With every project, our teams are committed to exceeding our customers’ expectations.
Products
Services
Ads
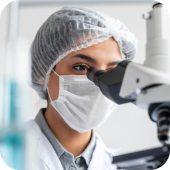
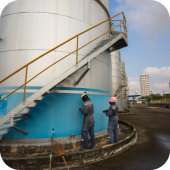
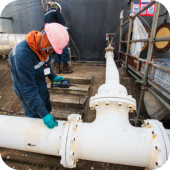