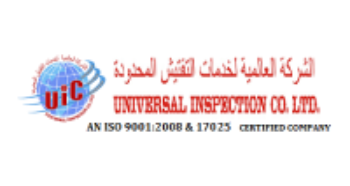
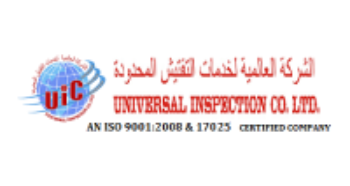
Universal Inspection Co. Ltd.
Universal Inspection Co. Ltd (UIC) is the World’s Leading Inspection, Calibration and testing Services Company headquartered in Jubail, Kingdom of Saudi Arabia.


Overview
Universal Inspection Co. Ltd (UIC) is the World’s Leading Inspection, Calibration and testing Services Company headquartered in Jubail, Kingdom of Saudi Arabia. Established in the year 2010, the company aims to provide outstanding quality assurance and quality control services to Oil and gas, Construction and Infrastructure, Power and Energy, Chemical Processing, Aviation and Defense, Electronics, Nuclear Power and manufacturing and other related industries around the world.
Universal Inspection Co. Ltd is an ISO 9001:2015 & ISO 17025: 2017 Accredited Company with branch offices in Riyadh, Jeddah, Dammam, Jizan, Yanbu, Turaif, Haradh, Safaniya, Duba and International Branches in Bahrain, Kuwait, Oman, India, Qatar and Malaysia. Till date, UIC has worked with more than 2000+ quality clients globally including reputed major firms such as SAUDI ARAMCO, NEOM, SABIC, ALBA-Bahrain, ORPIC-Oman, SEC, SATROP, SADARA, MARAFIQ, YASREF, MAADEN, SWCC, Saudi Railways, PetroRabigh, General Authority of Civil Aviation, Saudi Royal Commission, Petroleum Development of Oman (PDO), and many others.
Products
Services
Ads
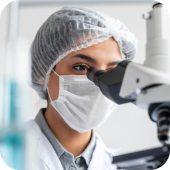
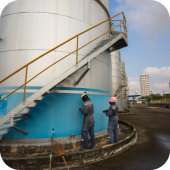
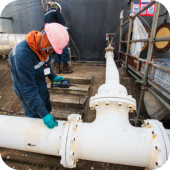