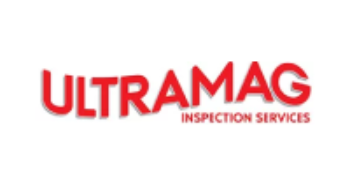
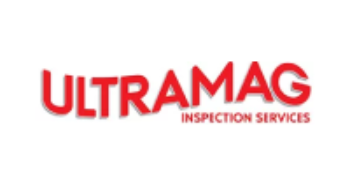
Ultramag Inspection Services
Ultramag Inspection Services Ltd is a market-leading, ISO 9001 and UKAS Accredited, independent Inspection Body providing inspection and testing services to a broad range of industries.


Overview
Ultramag Inspection Services Ltd is a market-leading, ISO 9001 and UKAS Accredited, independent Inspection Body providing inspection and testing services to a broad range of industries. Our main industries are Construction, Marine, Aerospace, Defence, Nuclear, Pressure Systems, Oil and gas, Power Generation and renewables. along with N.D.T. Training and Consultancy.
We have been providing a professional non-destructive and mechanical testing service for over 45 years. Our new facility is now open for N.D.T., Welder training, welding of test samples & mechanical testing of welder's test pieces. Our training department offers NDT courses, along with Welding Technology related courses and selected Safety courses.
Ultramag is a member of the British Institute of Non-Destructive Testing, Service Inspection Group, International Society for Condition Monitoring and an Associate Member of E.E.M.U.A. We hold Approvals from Lloyd's Register, Bureau Veritas, RINA, DNV-GL and the American Bureau of Shipping. Our inspectors hold qualifications for PCN, SNT, ACCP, CSWIP, NAS 410, EN 4179, AWS and IIW at Level 2 and 3.
Level 3 personnel ensure the smooth running of the facilities, with an I.I.W. Welding Technologist and Welding Specialists performing welding procedures, welder tests and welder training, along with guidance for RWCs of several clients on ISO 3834 standards.
Products
Services
Ads
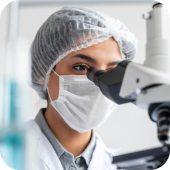
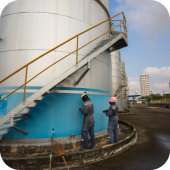
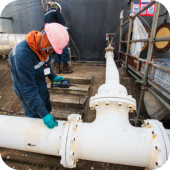