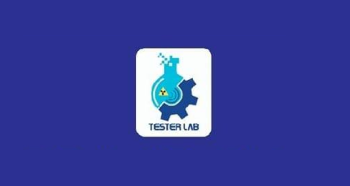
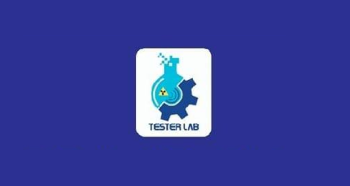
Tester Lab Private Limited
TESTER is National Accreditation Board For Testing and Calibration Laboratories (NABL) Accredited Laboratory. The NABL Certification number is TC-8520. We are specifically Accredited in Non Destructive Testing stream.


Overview
Tester has built and established a good reputation and is respected by its clients for the integrity and as well as reliability of its services. Tester persistently exceeds the expectations of our customers and satisfies their needs. Our primary goal is to integrate innovative new technologies and succeed in today’s competitive markets, upholding our mission of customer satisfaction. Following our vision, we pursue robust organizational growth. Key alliances with our good partners complement this strategy. We extend our presence into new markets and add selectively to our capabilities.
Products
Services
Ads
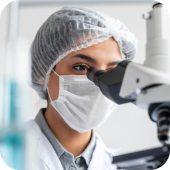
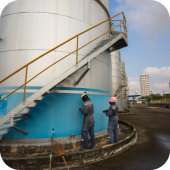
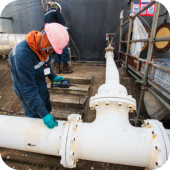