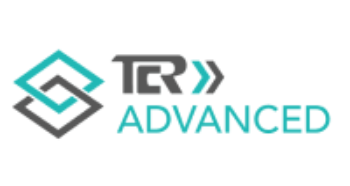
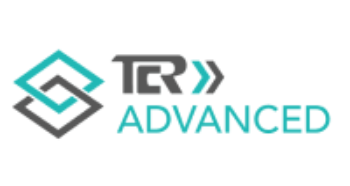
TCR Advanced Engineering Pvt. Ltd.
TCR has global expertise in life enhancement of different boiler and turbine by integrating knowledge of metallurgical degradation, corrosion and life-limiting factors


Overview
TCR Advanced Engineering is a service partner of TCR Engineering Services, a very reputed company established way back in 1973 by the great visionary late Sh. V. K. Bafna. TCR Advanced Engineering provides technical services in the area corrosion and metallurgy to the industries not only at Vadodara, a hub for chemical and petrochemical & fertilizer industries but also organizations world around. Company has a set-up comprising full-fledged advanced metallography and material characterization facilities at Vadodara, Gujarat.
TCR Advanced through its team of experts offers specialized services in the field of metallography and failure Investigation. The company provides asset integrity management, failure investigation of industrial plants and equipment, In-situ metallography, assessment of in-service degradation, components / parts indigenization, selection of materials, remaining life assessment (RLA) and fitness for service (FFS). TCR Advanced Engineering has a competent team of metallurgical and mechanical engineers, technicians and field staff working for in-house as well as on-site testing and investigation.
Mr. Paresh U. Haribhakti (Managing Director) who is a Metallurgical Engineer and holds Master degree in Material Technology heads the company. He is having vast experience of more than a two decades in the field of R & D activities, failure investigation, damage assessments and RLA studies at global level. TCR Advanced has set up a full-fledged advanced testing division at Vadodara to meet with the industries requirements for testing and material characterization such as raw material testing, material identification, microstructure examination for evaluation of material processing, chemical properties & physical properties of metallic materials. The testing division of TCR Advanced is NABL accredited as per international standard ISO/IEC-17025.
Products
Services
Ads
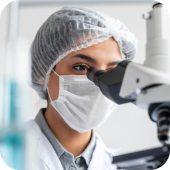
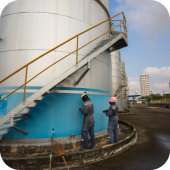
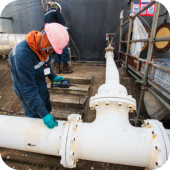