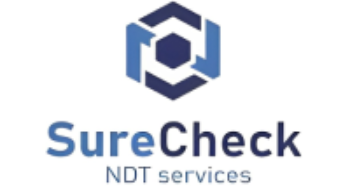
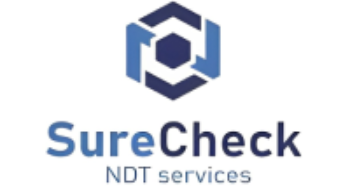
Surecheck NDT
Surecheck is a specialist industrial NDT company serving the fabrication & welding industry.


Overview
Surecheck is a specialist industrial NDT company serving the fabrication & welding industry.
Surecheck (Eurospection) has been around for more than 35 years servicing various industry sectors.
Surecheck has serviced oil, gas, and petrochemical industries to pressure vessel/pipework and structural sectors.
Surecheck also offers an NDT service to numerous mechanical test houses that are involved with the qualification of welding procedures and welder qualifications. Test results are usually available within 24 hours!
Surecheck offers on and off-site industrial x-radiography, magnetic particle testing, dye penetrant, and ultrasonic testing. All their staff hold PCN qualifications issued under ISO 9712 certification requirements and ASNT.
Products
Services
Ads
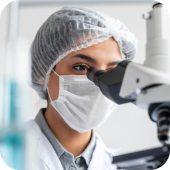
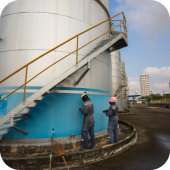
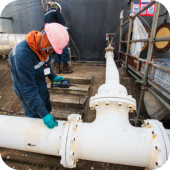