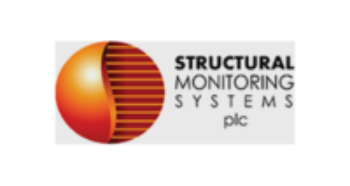
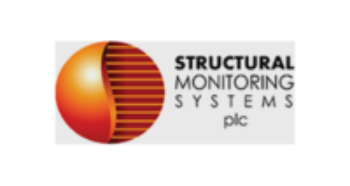
Structural Monitoring Systems
Structural Monitoring Systems is engaged in the development and commercialization of its CVM™ sensor technology


Overview
History shows a need for accurate, reliable, in-situ monitoring of the structural integrity of aircraft, bridges, pipelines, and buildings.
Once tested, a structure is assumed to be safe until the next inspection. However, much can occur to the structure before the next periodic test. Aside from this uncertainty, manual testing is a reoccurring, labor-intensive procedure that is subject to human error and misinterpretation.
Early techniques developed to assist manual inspection included visual & magnetic testing and dye penetration. These techniques were focused on surface defects only. Subsequent techniques such as x-ray, eddy current, and ultrasonic technologies could detect internal flaws in materials.
The need to monitor structures became known as Structural Health Monitoring, and it is in this category that Structural Monitoring Systems Comparative Vacuum Monitoring (CVM™) technology is the forerunner.
The aviation industry provides a great array of applications and programs for the full commercialization of the CVM™ technology platform. As such, SMS has undertaken and completed multiple civilian programs to gain full certification for the use of CVM™ from both regulators and key aerospace OEMs.
Looking ahead, CVM™ will aim to be the routinely accepted method for performing periodic, continual maintenance on all aircraft types worldwide.
Products
Services
Ads
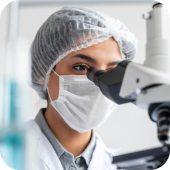
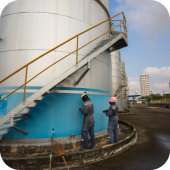
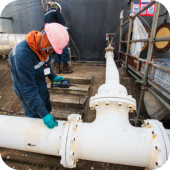