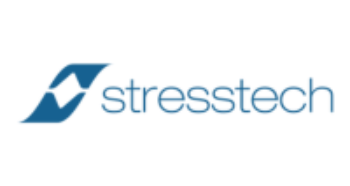
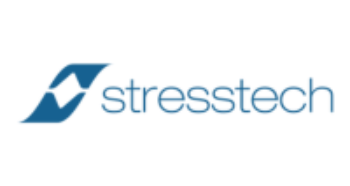
Stresstech
For more than 30 years, Stresstech has been providing non-destructive and destructive testing solutions for process control and quality inspection.


Overview
For more than 30 years, Stresstech has been providing non-destructive and destructive testing solutions for process control and quality inspection. Stresstech is headquartered in Finland and has offices in Germany, the United States, and India, as well as sales and service representatives around the world.
Roboscan measurement adjustment with user
Mission
Stresstech’s mission is to serve the quality control and material research needs of the manufacturing industry, research institutes and universities by providing testing equipment and knowledge. We have the knowledge and experience of our technologies all under one roof, from basic science to production. Our team of experts is committed to innovate, develop, and manufacture turnkey systems for:
residual stress measurement
heat treatment verification
grinding burn detection
Vision
Stresstech’s vision is to ensure that the manufactured components are sustainable, reliable, and safe. Our vision is to develop science-based quality control solutions so simple and effective that every manufacturer within our target market industries are willing to use one.
Customer value statement
With Stresstech solutions, you can improve and control the quality of your manufacturing processes, that can affect material properties.
Products
Services
Ads
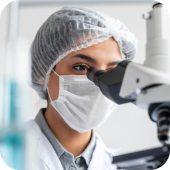
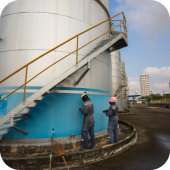
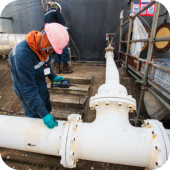