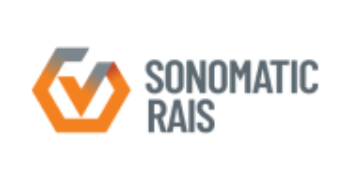
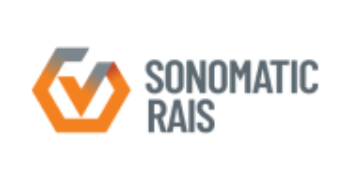
Sonomatic RAIS
SONOMATIC work with our clients to find and deliver solutions. Those solutions arrive from three places – Innovation, Technology


Overview
DELIVERING NDT TECHNOLOGIES. DIFFERENTLY.
SONOMATIC work with our clients to find and deliver solutions. Those solutions arrive from three places – Innovation, Technology and more importantly, a Team that believe in themselves and believes we can deliver better.
We develop strong partnerships with our clients, our vendors, our training companies, our hygiene engineers and fellow contractors. By opening up lines of open and honest communication with all parties, together we bring in projects safely, on time and very likely under or at budget.
Our thinking is diverse, our equipment belongs on the Starship Enterprise! and our enthusiasm and energy is what makes us so different to other companies. NDT is NDT. Physics is Physics. So we can all show up with the same equipment and do the same job, but SONOMATIC RAIS offer more. We offer open-minds, curious minds and a real passion and willingness to bring new life to old contracts, new dreams to new contracts – we offer a difference.
SONOMATIC represent the very best in skills and knowledge in conventional, advanced, specialised and engineering Inspection. But our delivery is different.
INSPECTION LEADERS
An image of Sonomatic RAIS inspectors
Sonomatic RAIS is part of a group of companies collectively known as the CWL Group, providing specialist access, inspection, maintenance and implementation services. Together the Group combined their individual strengths to bring a key group of people together offering a one-call solution service to our clients.
Inspection has many parts to it – depending on the required outcome, we provide options from the simplest of Inspections to the most complex and we can do it from a rope, using robots, crawlers, on land, offshore and sub-sea. But what we do differently, is complete our own surface preparation using our patented laser cleaning system.
Through one contact point, the CWL Group covers every single step of that process, our access teams get us into places safely and securely, and our patented laser system performs surface preparation helping our client avoid thousands of downtime hours, with no damage to the existing substrate, no mess, and does almost zero harm to the planet!
Let us take the problem – we have the skills and knowledge in conventional, advanced, specialised, subsea and engineering Inspections to find you the right solution.
You will find the very best people, real people who can connect with your issue and work hard to provide the best solution, if it is a one-day job that can be done by a sole Level 1 Tech, that is exactly what we will offer if we believe the project will need a team of five or ten, or whatever we deem to be the best all-round solution for our client, we will explain why and exactly what you can expect results wise and costs wise to justify such a team.
Products
Services
Ads
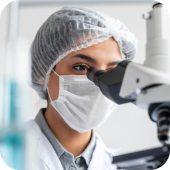
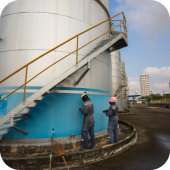
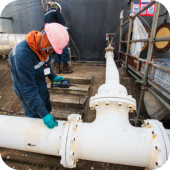