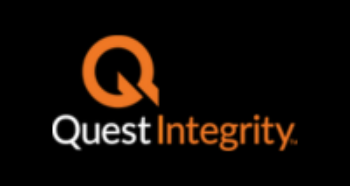
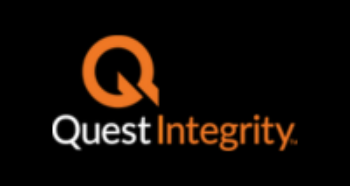
Quest Integrity Group
Quest Integrity carries the legacy of a preeminently successful, long-established technology incubator based in the Pacific Northwest.


Overview
Quest Integrity carries the legacy of a preeminently successful, long-established technology incubator based in the Pacific Northwest. One of many spinouts over the years, Quest Integrity was originally formed as a joint venture between Quest Integrated and Koch Industries in 2004. Now part of Baker Hughes, Quest Integrity is further expanding its suite of unique inspection technologies coupled with a passion to apply advanced computational mechanics models to empower superior decision making by its valued customers.
Products
Services
Ads
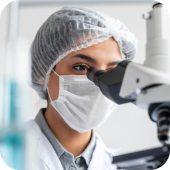
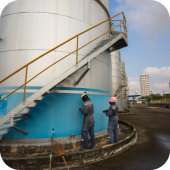
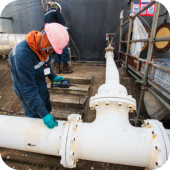