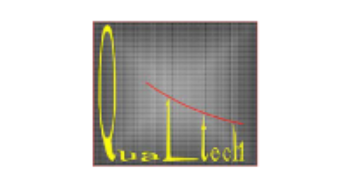
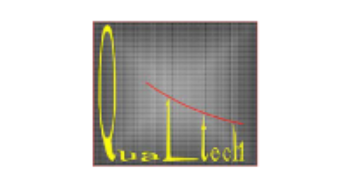
Qualtech NDE
Qulatech NDE is pleased to introduce our services as one of the newly established inspection companies in the field of NDT, enjoying a good reputation for timely completion of projects and quality workmanship. All inspection activities performed by us are through our in-house resources.


Overview
Qualtech NDE is pleased to introduce our services as one of the newly established inspection companies in Non-Destructive Testing (NDT), enjoying a good reputation for timely completion of projects and quality workmanship. All inspection activities performed by us are through our in-house resources.
Their qualified engineers and inspectors with a devoted team of workers have completed several challenging works and satisfied the clients with their professional and sincere services. Their experienced and trained engineers always fulfil their commitment within a scheduled time amid safety and quality. They assure you that they can perform complete NDT inspection of storage tanks, steel structures, power plant turbines & generators, pipeline welds, and process industry components, backed by highly professional skills, capable technical staff, equipment and inspection procedures.
Products
Services
Ads
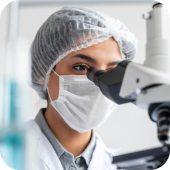
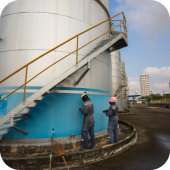
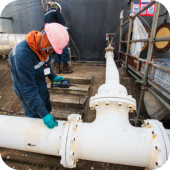