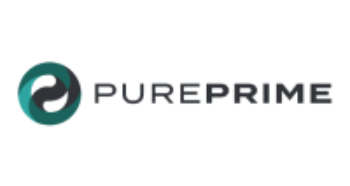
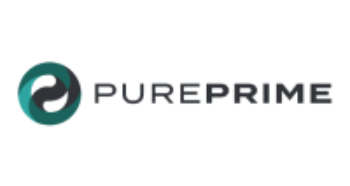
Pure Prime Solutions
Pure Prime Solutions (PPS) is a team of experts with deep knowledge in engineering design, simulation, analysis, and testing.


Overview
As digital technology transforms your industry, it's up to you to stay on top of the trends before your competitors do.
Pure Prime Solutions can help you gain a competitive advantage by leveraging the digital transformation and approaches used in industry 4.0 technology.
Pure Prime Solutions are the industry experts in simulation, system integration, product lifecycle, and digital twins. Their designs may take more time upfront but are worth every penny in reduced maintenance costs, improved manufacturing throughputs, greater quality consistency, and higher customer satisfaction.
Products
Services
Ads
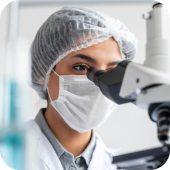
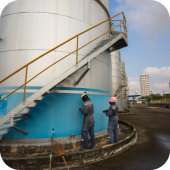
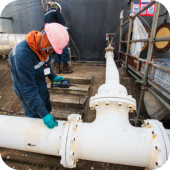