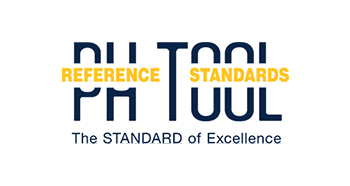
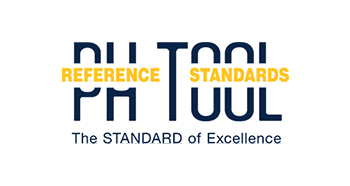
PH Tool Reference Standards
Meeting the demands of the increasingly complex and quality-conscious NDT marketplace is a challenge we gladly accept.


Overview
PH Tool Reference Standards, headquartered in Pipersville, PA, has supplied the Nondestructive Testing (NDT) industry with high quality Reference Standards and Test Blocks since its founding by Phil Herman Sr. in 1973. Whether you need EDM notches, Flat-bottom holes, Micro-holes, or Test Blocks, PH Tool can handle your order.
The entire staff of skilled toolmakers, machinists, technicians, and professional management personnel is dedicated to the development and manufacture of the finest quality Reference Standards available today. Our robust growth and excellent reputation in the NDT world can be attributed to our emphasis on quality, attention to detail, and innovative approaches to the most challenging requirements of our valued customers.
Meeting the demands of the increasingly complex and quality-conscious NDT marketplace is a challenge we gladly accept. We welcome your inquiries and look forward to serving you.
Products
Services
Ads
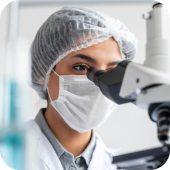
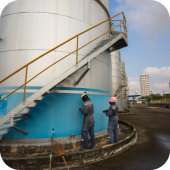
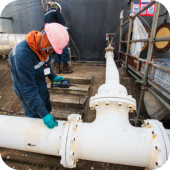