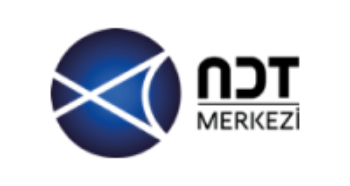
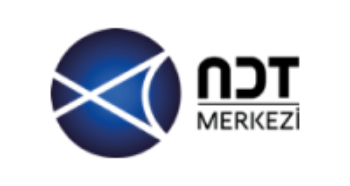
NDT CENTER
NDT CENTER was established in 2019 by observing the needs of the welded manufacturing, casting and forging sectors and to provide development, training, and certification according to international standards and inspection services of the personnel who will perform inspection in these sectors.


Overview
NDT CENTER was established in 2019 by observing the needs of the welded manufacturing, casting and forging sectors and to provide development, training, and certification according to international standards and inspection services of the personnel who will perform inspection in these sectors.
We offer Personnel Certification and Industrial inspection services by international standards and legal regulations with our understanding of total quality, our human and environment-oriented working principle, our principle of independence and impartiality, and our expert personnel whose professional development is constantly supported by our institution with up-to-date training.
NDT CENTER provides services in areas such as welder training, non-destructive testing training and certification, training and certification of welders, and welding engineering services to manufacturing organizations. NDT CENTER serves with modern laboratories and devices, non-destructive testing and welder training with specialized personnel.
Products
Services
Ads
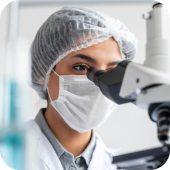
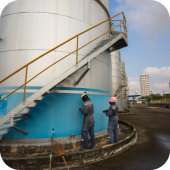
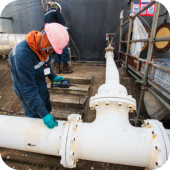