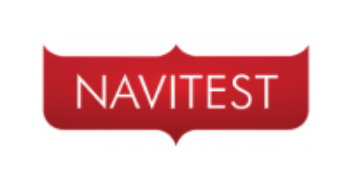
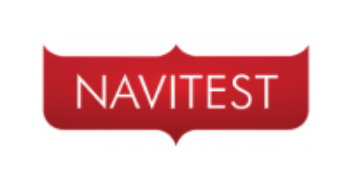
Navitest
Navitest Sp. z o.o laboratory is the leader in the field of non-destructive tests in Northern Poland.


Overview
Navitest Sp. z o.o laboratory is the leader in the field of non-destructive tests in Northern Poland. Based on more than thirty years of experience, we can provide our clients with sure, safe and timely services. With a whole range of tools and highly qualified specialists, we offer non-destructive tests and thickness measurements for all kinds of clients and trades. Check out our possibilities and the profile of our company. Tell us what you need.
We offer the highest level of services in the shortest time possible. To achieve this we have adequate resources, both in equipment and personnel. If such a need arises, we service our business partners seven days a week. Equally quickly we issue the reports from our test in a form corresponding to that requested by our clients. We perform our tests following Polish, European, ISO and ASME standards, Classification Societies rules, NORSOK requirements and any other specifications provided by our clients.
Products
Services
Ads
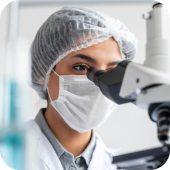
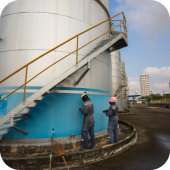
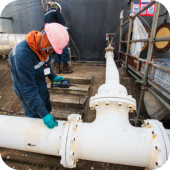