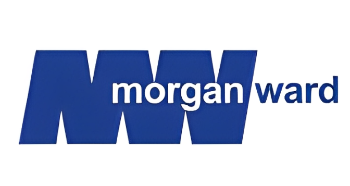
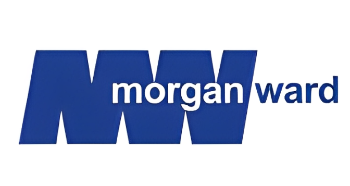
Morgan Ward NDT Ltd.
Morgan Ward have been leaders in non-destructive testing for almost fifty years and continue to offer top-quality inspection services to a vast range of industries, both in the UK and abroad.


Overview
Morgan Ward NDT is one of the world’s leading providers of non-destructive testing, inspection and advisory services to the aerospace, petrochemical, defence and general engineering industries.
Our highly skilled team of specialist technicians are based at various locations across the UK but offer on-site inspection throughout the UK and the rest of the world.
We have extensive experience supplying personnel and consultancy services for global assignments and international projects.
Morgan Ward have been leaders in non-destructive testing for almost fifty years and continue to offer top-quality inspection services to a vast range of industries, both in the UK and abroad.
The company and its individual technicians carry an extensive range of national, international and customer approvals and certifications.
We deliver an exceptional and efficient, fully certified NDT service to all branches of global industry.
We are NADCAP approved NDT company with 3 facilities in the UK, Prestwick, Manchester and Stansted, covering all the traditional NDT methods together with the more advanced Phased Array UT, Thermography. We also hold CAA and FAA approval for aircraft inspections together with many prime and carrier approvals.
Products
Services
Ads
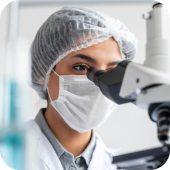
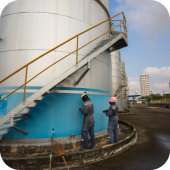
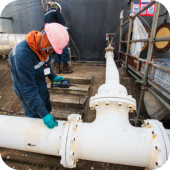