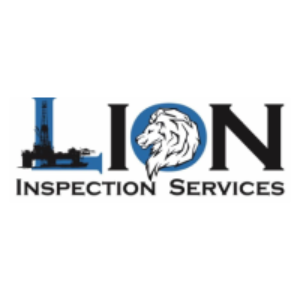
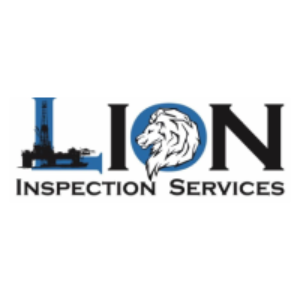
Lion Inspection Services
Lion Inspection Services is a leading NDT inspection company for the Oilfield Industry, established by M. Sierra with more than 25 years of experience in downhole drilling motors, shock subs, jars and other equipment used in the oilfield.


Overview
Lion Inspection Services is a leading NDT inspection company for the Oilfield Industry, established by M. Sierra with more than 25 years of experience in downhole drilling motors, shock subs, jars and other equipment used in the oilfield.
Lion Inspection Services also has experience with:
- EMI Drill Pipe Inspection
- Clean, Talley, and Drift Casing
- BHA Inspection
- Downhole Tools Inspection
- Downhole tools services and consulting
- 3rd Party / Cat V Inspection
Products
Services
Ads
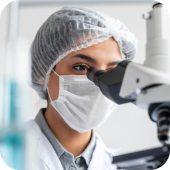
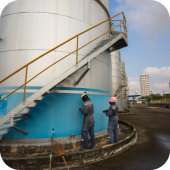
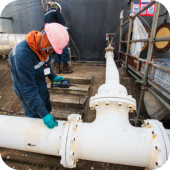