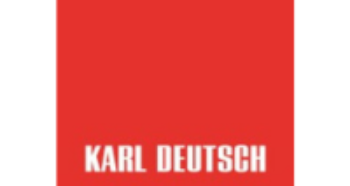
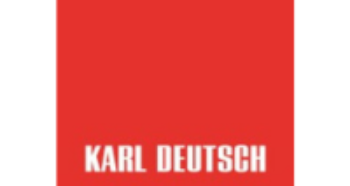
KARL DEUTSCH
The privately owned company KARL DEUTSCH was founded in 1949 and develops and produces instruments for non-destructive material testing.


Overview
Welcome to KARL DEUTSCH
The privately owned company KARL DEUTSCH was founded in 1949 and develops and produces instruments for non-destructive material testing. Portable instruments, stationary testing systems, sensors and crack detection liquids are produces by 130 motivated employees in two works in Wuppertal. Additional 20 employees in international offices and a worldwide network of dealers support the export business which accounts for more than 50% of the turnover. Our customers are metal producing and processing industries, e.g. steel works, automotive companies and bearing manufacturers. Typical test tasks are ultrasonic weld testing, detection of shrink holes in castings, crack detection in forgings with magnetic particles and dye penetrants, safety components for railway and aerospace as well as the wall and coating thickness measurement.
Products
Services
Ads
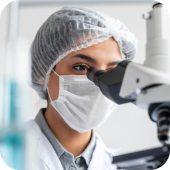
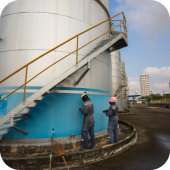
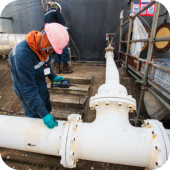