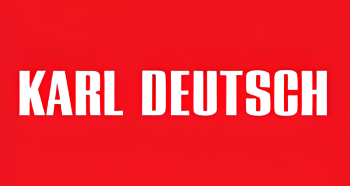
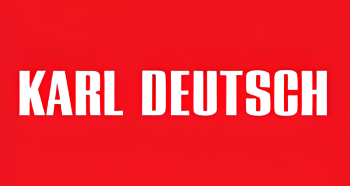
KARL DEUSTCH
The company KARL DEUTSCH was founded in 1949 and is currently managed by the third generation. It deals with the development and manufacture of equipment for non-destructive material testing (NDT).


Overview
A success story for more than 70 years
The company KARL DEUTSCH was founded in 1949 and is currently managed by the third generation. It deals with the development and manufacture of equipment for non-destructive material testing (NDT).
Mobile testing and measuring devices, stationary testing systems, sensors and chemical crack detection equipment are manufactured at two sites in Wuppertal by 130 motivated employees. Another 20 employees in foreign offices and a worldwide subsidiary network support the export business, which accounts for more than 50 % of sales.
Our customers are mainly from the metal producing and processing industry. Steelworks, suppliers to the automotive industry such as forges and foundries and manufacturers of ball bearings are important customers. Typical inspection tasks comprise weld seam inspection and the detection of casting cavities with ultrasound. Surface crack testing on forged parts is carried out using magnetic particles and the dye penetrant method. Safety parts for rail transport and aviation are also examined by means of NDT. Portable measuring instruments for wall and coating thickness measurement as well as for field strength and crack depth measurement complete the product range.
The company is rooted in Wuppertal in the region Bergisches Land. The deep connection to the city and area is actively lived. This includes extensive commitment to numerous projects that make the city more liveable. Examples are the “Nordbahntrasse” bike track and the Junior Uni.
Flexible and customer-oriented
Our mobile testing devices, stationary testing systems, sensors and chemical crack detection equipment are developed and manufactured in two plants in Wuppertal.
Specialists in the fields of UT, MT and PT work daily to further improve our products which have been established for years. Based on close interaction of the individual production areas, we offer our customers tailor-made technical solutions.
The concentration of all important production steps from purchasing, warehousing and production to sales and service enables short distances and flexible optimization.
Certification and testing of portable devices, for instance in the context of quality assurance requirements, is carried out quickly and easily in-house and usually takes not more than 4 days. Even with complicated tests, it takes a maximum of about 10 days before the device is ready for use again.
Customer service is a top priority for us: Nearly all technical questions about our products are answered by our application technology laboratory. The proximity to production and development enables us to provide the greatest possible customer orientation.
Products
Services
Ads
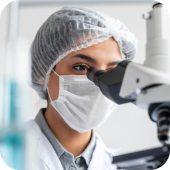
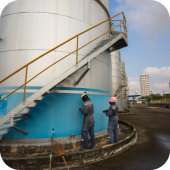
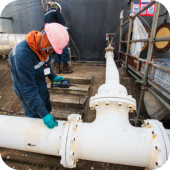