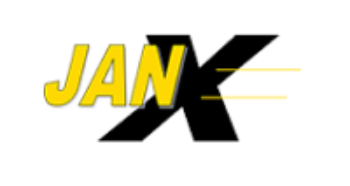
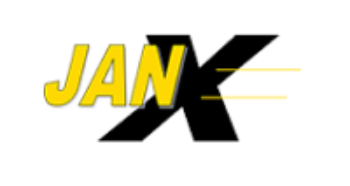
JANX
During the 41+ years that we have been in the non-destructive testing (NDT) and non-destructive evaluation (NDE) field, we’ve built and maintained a reputation for reliable, responsive service.


Overview
During the 41+ years that we have been in the non-destructive testing (NDT) and non-destructive evaluation (NDE) field, JANX built and maintained a reputation for reliable, responsive service.
For the 785 clients they worked with during the last several decades, that devotion to excellence, coupled with extensive experience and knowledge, has consistently resulted in the precise, accurate, and timely data they needed to effectively manage and protect their assets.
Today, JANX provides NDT and NDE in 43 of the country’s 50 states. And with every project, on every scale, we stand behind our work.
The JANX Difference
- The capacity to staff up quickly—we report to work sites within 24 to 48 hours of service calls, often in less time.
- A full-time staff of mechanics who build onsite darkrooms and retrofit our trucks for your project’s requirements to make sure you get prompt, effective service.
- 350+ vehicle fleet with no vehicles older than five years old, so you can count on us to get where you need us, on time and ready to work.
- Conventional and cutting-edge evaluation methods, including the use of proprietary and highly advanced technologies.
- Knowledgeable technicians and team leaders with an extensive understanding of our customers’ needs and the industries we serve.
- A relationship-based approach to business—many of our customers have been with us for years, and several have been returning to JANX since we were founded in 1981.
Products
Services
Ads
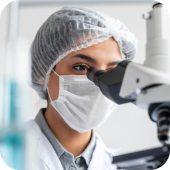
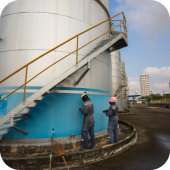
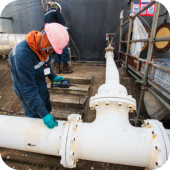