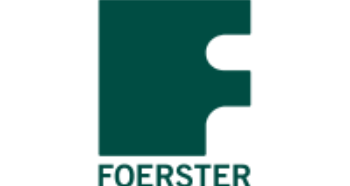
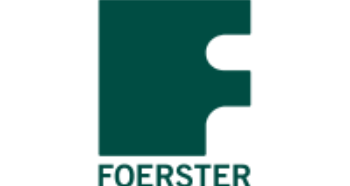
Institut Dr. Foerster GmbH & Co. KG
The name FOERSTER has stood for the highest quality and precision since 1948. We develop and produce devices


Overview
The name FOERSTER has stood for the highest quality and precision since 1948. We develop and produce devices and systems for non-destructive testing of metallic materials, metal detection and magnetics.
As a technology leader, we make surface defects visible with electromagnetic test methods such as eddy current or leakage flux testing, but also with ultrasound and inductive heat flow thermography. With highly sensitive fluxgate magnetometers, our detection devices also precisely localize contaminated sites, UXO and archaeological artefacts. Devices for determining magnetic properties and for testing the hardness of metallic components complete our comprehensive portfolio.
In addition to the development of individual devices, our expertise lies in the implementation of complete, customer-specific test lines and their automation. With our business solutions, we also offer you extensive services. We see ourselves as a partner for the entire product life cycle: from development to design and production to service and training.
With a qualified sales and service network, we are active for you in more than 60 countries worldwide.
Products
Services
Ads
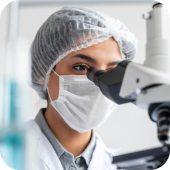
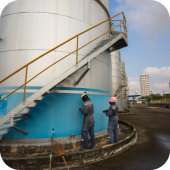
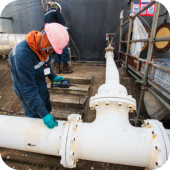