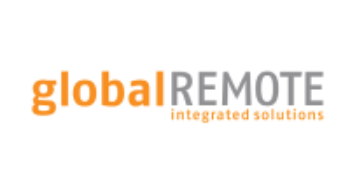
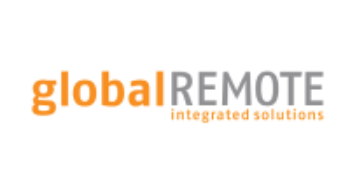
Inside Exploration Technologies
Global Remote services has a growing global client base, delivering a comprehensive range of services to the energy, civil, marine, and geotechnical sectors.


Overview
Company Profile
Founded in 2007, Global Remote Services has a growing global client base, delivering a comprehensive range of services to the energy, civil, marine, and geotechnical sectors. Global Remote Services offers value and flexibility to meet all their client’s demands, centered around the cost-effective and efficient management of their multi-disciplined and internationally experienced personnel across the globe. Global Remote Services global service capability stems from their expanding geographical presence, servicing India, the Middle East, West Africa, and Central and South East Asia via their regional and partner offices in Azerbaijan, Bahrain, India, Iraq, Kazakhstan, Oman, Qatar, Turkmenistan, UAE, and the USA.
Mission
Global Remote is a company founded on the core principles of integrity, safety, and quality. Global Remote endeavors to provide innovative, efficient, and cost-effective solutions to all their clients, regardless of project complexity, environment, or location. Global Remote Services values its reputation and strives to maintain it!
Group Companies
Jacob Inspection Services
- Asset integrity management and risk-based inspections
- Plant inspection and shutdown survey
- Shutdown and turnaround projects
- Third-party inspection and advanced non-destructive testing
- Specialised human resource management
Inside Exploration Technologies
- Technical training (NDT, API, ASME)
- Technical events workshops and conferences
- Accredited by API, ASNT, and ASME as a training provider
Products
Services
Ads
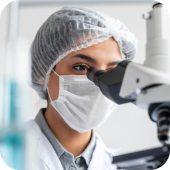
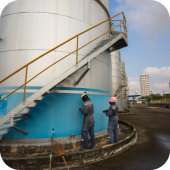
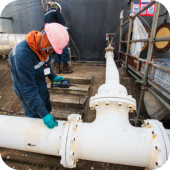