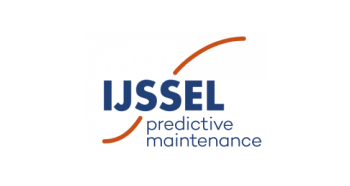
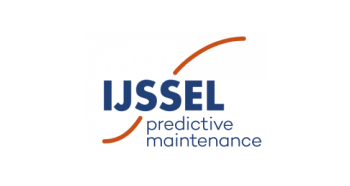
IJssel Predictive Maintenance
We are IJssel. We have been making smart factories since 1993. We realize, maintain and improve factories with the aim of keeping the industry in the Netherlands in a sustainable way. Every production company has its own specific issues.


Overview
Continuous improvement, that's what we're good at at IJssel. You can even call it our passion. We improve production processes and results for many great clients. Always together, as your partner in smarter production, and always based on the IJssel model.
With IJssel Technology you get more return from production.
Today better than yesterday, and tomorrow better than today. We have lived up to this credo since 1992, together with our clients. We standardize, optimize and innovate, especially in manufacturing companies. Not at a distance, but always together and as part of your organization.
We can also implement, maintain and continuously improve the smart solutions that we devise together. After all, in addition to clever heads and organizational talent, we also have clever hands. From business experts to mechanics, IJssel has them of the highest level. A unique combination in the sector.
Products
Services
Ads
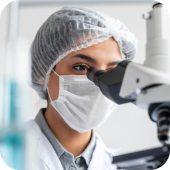
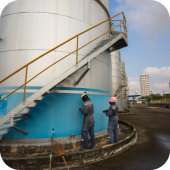
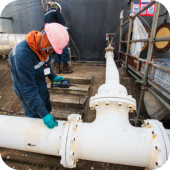