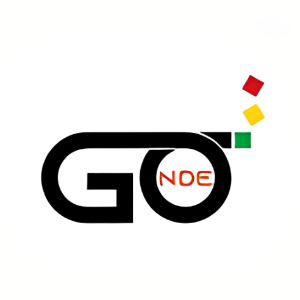
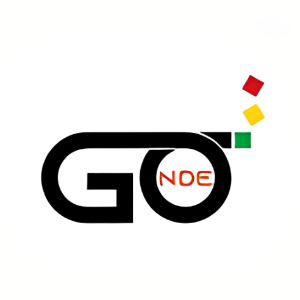
Guyana Oil NDE
GO NDE Inc. is a joint venture partnership between Guyana Oil and Gas Support Services Inc. and Non-Destructive Testers Guyana Inc.


Overview
GO NDE Inc. is a joint venture partnership between Guyana Oil and Gas Support Services Inc. and Non-Destructive Testers Guyana Inc.
GO NDE Inc. is a majority Guyanese-owned - Guyanese Registered company. GO NDE Inc. has engaged experienced and skilled professionals committed to the growth and development of Guyana’s Oil and Gas Sector.
Mission
To deliver quality services to our clients in a safe manner that defines dependability and excellence through a blend of state-of-the-art technology, tools, and qualified personnel.
Vision
To become the leading provider of Inspection, Access, and Training services in Guyana and the region allowing for a sustainable workplace and satisfied stakeholders.
Values
- Operate with integrity.
- Client-focused, success-driven
- Innovative, problem-solving.
- Inclusive work culture
- Foster a rewarding workplace.
- Reduce carbon footprint.
Products
Services
Ads
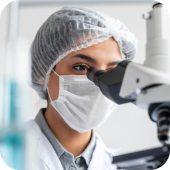
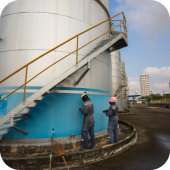
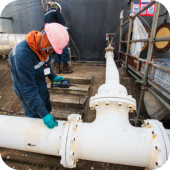