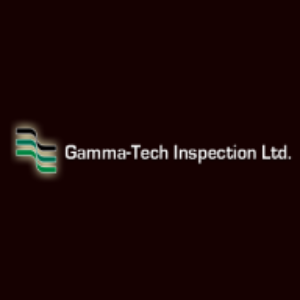
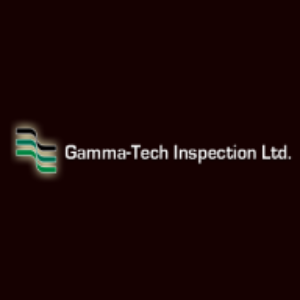
Gamma-Tech Inspection Ltd.
Gamma-Tech has aspired to achieve a level of customer care unheard of in the NDT industry and the results speak for themselves.


Overview
Gamma-Tech Inspection Ltd. (GTIL) has put customer care first. Founder and current owner Debra Ross knew that NDT clients were eager for a company capable of promptly providing the highest quality testing services and at a reasonable price. Gamma-Tech has aspired to achieve a level of customer care unheard of in the NDT industry and the results speak for themselves.
Gamma-Tech’s commitment to customer service is supported by our dedication to understanding our client's needs, function, quality assurance and safety programs that encompass state-of-the-art equipment and technology. With a first-rate reputation, Gamma-Tech provides a full suite of NDT services to the oilfield and construction industry. We proudly cater to a long list of loyal clients.
Since its founding in 2002, Gamma-Tech has continuously increased its expertise and experience in all aspects of our industry, providing service based on the latest technology and equipment available to its clients.
Products
Services
Ads
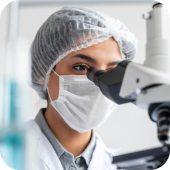
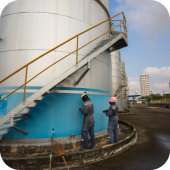
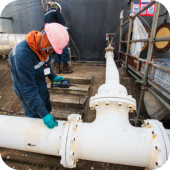