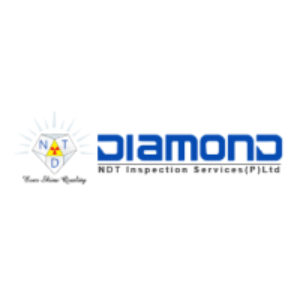
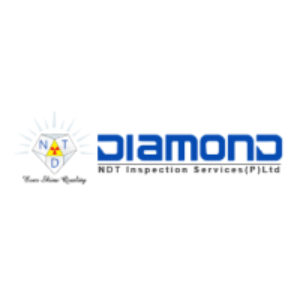
DIAMOND NDT INSPECTION SERVICES PRIVATE LIMITED
Diamond NDT Inspection Services, was established in 2011 it expanded its operations to offer Non-Destructive Testing (NDT) services, NDT Training and Certification


Overview
- NDT Training & Certification
- NDT Inspection Services
- Radiography Testing ( RT)
- Phased Array Ultrasonic Inspection (PAUT),TOFD
- Positive Material Identification ( PMI)
- Digital Hardness Testing ( DHT - Portable)
- Ultrasonic Thickness Gauge ( UTG)
- Ultrasonic Testing ( UT)
- Liquid Penetrant Testing ( LPT)
- Magnetic Particle Testing ( MPT)
- Eddy Current Testing ( ET)
- Visual Inspection ( VT)
- Surface Inspection
- Third Party Inspection Services
- Welder Training & Certification
- WPS/PQR/WQT Consultancy & Certification
Products
Services
Ads
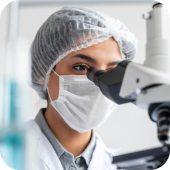
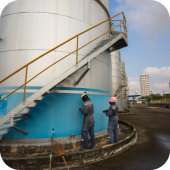
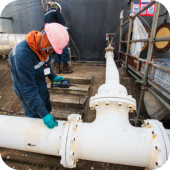