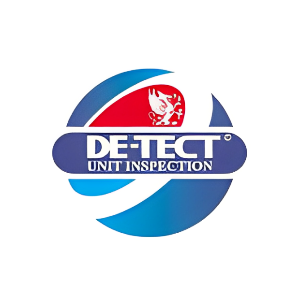
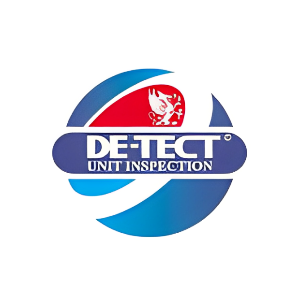
De-Tect Unit Inspection (Pty) Ltd
We are worldwide leaders in Specialist Inspection, Non Destructive Testing and Heat Treatment services.


Overview
We are worldwide leaders in Specialist Inspection, Non-Destructive Testing and Heat Treatment services. Our mission is to provide our clients with a full range of quality and trusted services that can successfully take them from design and engineering to resourcing and execution. We are committed to excellence since 1980 and will continue to improve while providing the most cost-effective and high quality solutions to our clients using the latest cutting-edge technologies, equipment and highly trained and qualified personnel.
Products
Services
Ads
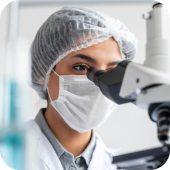
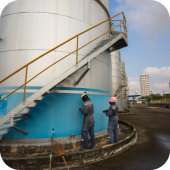
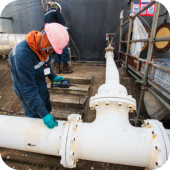