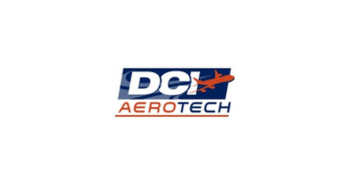
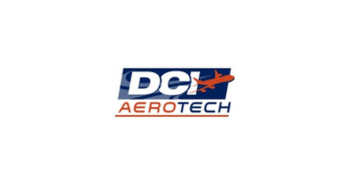
DCI Aerotech
DCI Aerotech offers plating, non-destructive testing, robotic shot peen, prime & paint, chrome grind and our most recent addition robotic HVOF coatings and grind.


Overview
DCI Aerotech originally started as a single-building WWII chromium plating shop supporting President Franklin D. Roosevelt’s “Arsenal of Democracy”. DCI Aerotech now encompasses 6 buildings, 160,000 square feet and over 100 Nadcap approved process.
DCI Aerotech offers plating, non-destructive testing, robotic shot peen, prime & paint, chrome grind and our most recent addition robotic HVOF coatings and grind.
DCI Aerotech is categorized as FAA repair station D77R737Y.
DCI’s overhaul capabilities range from landing gear components to P&W turboprop engines to Boeing ball screws and actuators
HVOF, Chrome Plate, NDT, MPI, FPI, Robotic Shot Peen, Paint, Chrome/HVOF Grind, Temper(Nital) Etch, Sulfamate Nickel Plate, LHE Cadmium Plate, LHE Zinc-Nickel, Titanium-Cadmium Plate, Silver Plate, Nickel Cad Diffused, Lead-Tin, E-Nickel Plate, Zinc Plate, Chemical Conversion Coating, Zinc Phosphating, Manganese Phosphating, Titanium Phosphating, Bronze Plate, Copper Plate, Indium Plate, Titanium Anodize
Products
Services
Ads
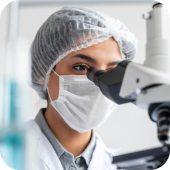
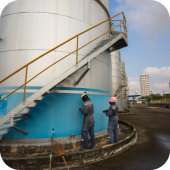
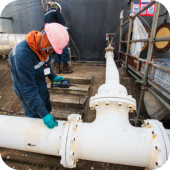