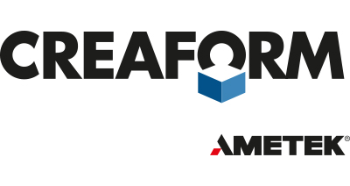
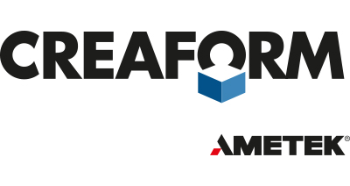
Creaform
We are on fire, driven by the conviction that nothing is impossible. We invest ourselves heart and soul to transform the projects we imagine into reality. We trace our future road with pride and enthusiasm.

Overview
Boasting two decades of experience shaping the future of dimensional metrology, Creaform assists their customers achieve their measurement ambitions through cutting-edge 3D solutions. With its extensive hardware and software portfolio, Creaform enables its users to experience innovation firsthand through 3D scanning, reverse engineering, quality control, non-destructive testing, product development, and MRO. Thousands of professionals in various industries, like automotive, aerospace, manufacturing, heavy industries, oil and gas, power generation, consumer products, research and education, have discovered that with Creaform, Innovation Takes Form.
Headquartered in Lévis,
Québec, Creaform is present in more than 85 countries, through its 26 locations
all around the world and a network of over a hundred distributors. A presence
that enables the company to build relations and provide unmatched customer
service. Creaform is a business unit of AMETEK, Inc., a leading global provider
of industrial technology solutions serving a diverse set of attractive niche
markets with annual sales of over $7.0 billion
Products
Services
Ads
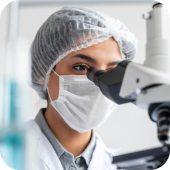
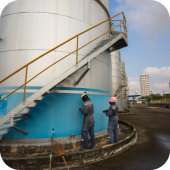
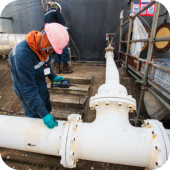