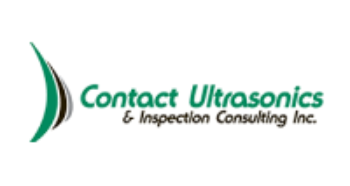
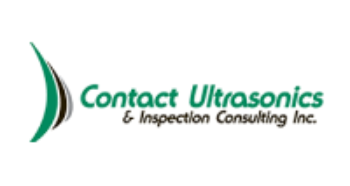
Contact Ultrasonics & Inspection Consulting Inc.
Contact Ultrasonics & Inspection Consulting performs upstream and downstream industrial inspections to provide their clients.


Overview
Contact Ultrasonics & Inspection Consulting performs upstream and downstream industrial inspections to provide our clients with quick, accurate, & reliable information along with the documentation for records of all inspections performed to ensure code compliance. All inspections are performed by American Welding Society Certified Welding Inspectors (AWS / CWI), American Society For Nondestructive Testing Level III technicians, or Level II technicians certified by company procedures that meet the requirements of ASNT recommended practice SNT-TC-1A. Reports can be completed and delivered electronically or handwritten.
Our technicians have many years of field experience performing structural integrity, safety, and nondestructive inspections in industries including:
Drilling Rigs (Land & Offshore) – Contact Ultrasonics performs API-4G inspections on masts or derricks, and API-Section 8 inspections on drilling tools by the American Petroleum Institute recommended practices. We perform structural integrity inspections, looking for stress cracking, on all drilling rig components including the mast/derrick, substructure, high-pressure mud lines, mud pumps, mud tanks, shaker skid, etc. We also perform safety inspections for OSHA compliance.
Chemical & Petrochemical Plants: Contact Ultrasonics performs On-Stream and Turnaround / Outage NDT inspections, for the plant inspection department or maintenance contractors, on various components including (but not limited to) piping, pressure vessels, heat exchangers, and storage tanks.
Products
Services
Ads
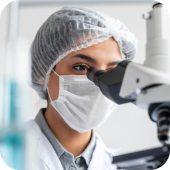
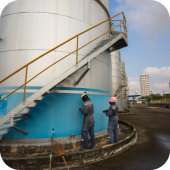
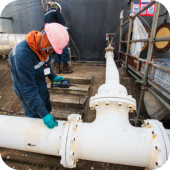