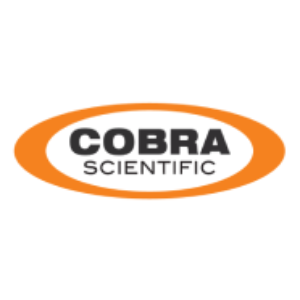
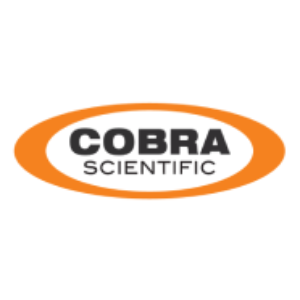
Cobra Scientific, LLC
Cobra Scientific LLC, manufactures and integrates automated and manual non-destructive test equipment and fixtures to assist with Ultrasonic and Eddy Current NDT (non-destructive testing)


Overview
Cobra Scientific, LLC, manufactures and integrates automated and manual non-destructive test equipment and fixtures to assist with Ultrasonic and Eddy Current NDT (non-destructive testing) in the Aerospace, Oil and gas, and Power Generation as well as other non-aligned industries. These systems typically incorporate various levels of Motion Control and Data Acquisition to Data Analysis.
Technologies we have implemented include multi-axis, robotic, Ultrasonic Flaw Detection Systems (conventional and phased array) as well as Eddy Current single point and array-based inspection systems.
Several of our Inspection Systems were “blind inspections”, incorporating an element of AI to self-acquire unseen and relatively undefined geometries, then self-define a scan contour, removing sample tolerance issues and setting in place a self-taught inspection profile.
Cobra Scientific works to develop the most cost-effective solution for your application. Cobra Scientific takes the time to discuss with you and understand the desired inspection outcome. Then they look across to the available technology base and, incorporate our own internal Engineering, Applications, and Manufacturing abilities to provide a comprehensive approach to a given application. When necessary, we will work with our recommended vendor(s) in an element of system design, be that an electronic instrument or custom software development including multi-axis motion control, data acquisition, and comprehensive data analysis software allowing the user to dig even deeper into their data sets.
With our broad-based knowledge of NDT Technologies, we are positioned to provide our customers with end-to-end solutions working with a broad range of equipment manufacturers across the industry where required.
Products
Services
Ads
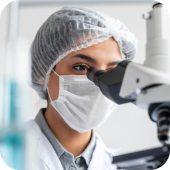
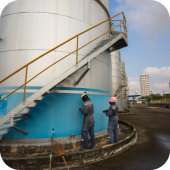
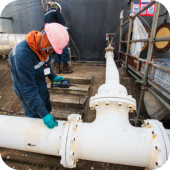