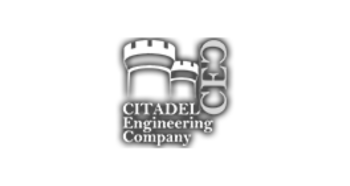
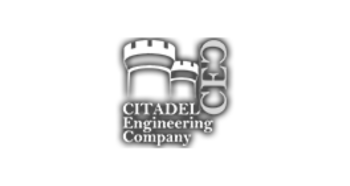
Citadel Engineering Company
Citadel Engineering Services was originally incorporated in the USA in 2015 as Engineering, Calibration & Inspection Body

Overview
Citadel Engineering Services was originally incorporated in the USA in 2015 as Engineering, Calibration & Inspection Body. After initial involvement in several development projects inside the USA and Europe, CEC started business in the early days of oil exploration in the Kurdistan Region, CEC was contracted as one of the 1st Calibration and Inspection Bodies in Iraq and the Kurdistan Region.
Established in 2015, CITADEL transformed grain trading in the United States, by offering innovative Engineering and inspection services. The Company was registered in the United States as a United Citadel Engineering Company but the name changed to Citadel Engineering Company (CEC) in 2019 and registered as TradeMark in several companies around the world.
CITADEL Engineering Company (CEC) has more than 5 offices inside the USA and more than 10 officers internationally and more than 250 employees.
The current structure of our company consists of 5 business segments operating across 4 Geographical Regions and more than 5M USD in Revenue.
We have done this through continual improvement and innovation and through supporting our customers’ operations by reducing risk and improving productivity. Citadel Engineering has a history of providing leadership and innovation in performance improvement.
Products
Services
Ads
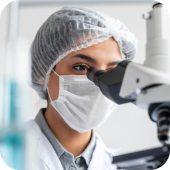
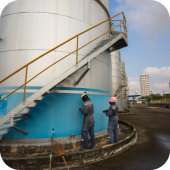
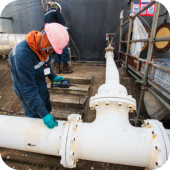