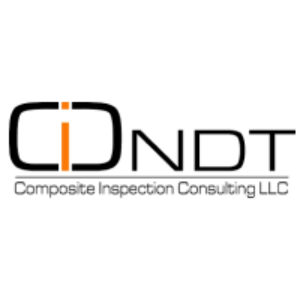
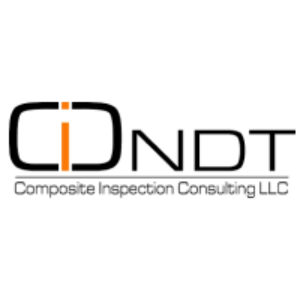
CICNDT LLC
At Composite Inspection and Consulting LLC, they aim to be flexible and focused on the customer's needs.


Overview
At Composite Inspection and Consulting LLC, they aim to be flexible and focused on the customer's needs. Too often you see third-party consulting companies take advantage of a customer who doesn't understand the ins and outs of NDT. CICNDT strive to give the customer only what they need but at the same time look out for them making sure they can meet future needs as well. They love what they do and hope it shines through in their work.
Products
Services
Ads
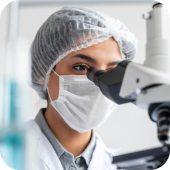
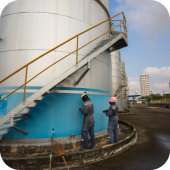
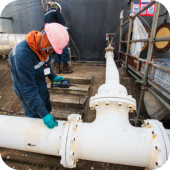