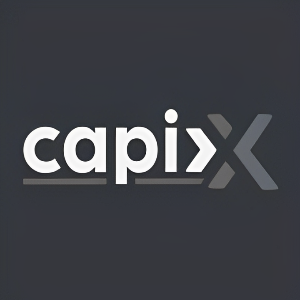
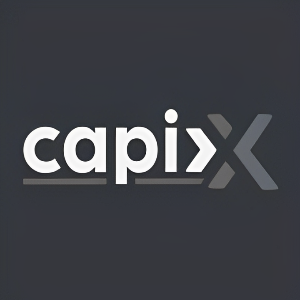
Capix
Capix Ltd is a long established, High Profile Supplier of Professional Film and Paper Processing equipment and Contract Support Services within The UK and Ireland.


Overview
Welcome to Capix
Capix Ltd is a long established, High Profile Supplier of Professional Film and Paper Processing equipment and Contract Support Services within The UK and Ireland.
We Offer a comprehensive range of equipment from Colenta Labortechnik in Austria for the processing of Photographic, PCB, Industrial (NDT) and Medical X-Ray Media, as well as related ancillary equipment.
Established in 1987 we have over 30 years of experience and offer a truly inclusive service from equipment supply to installation and service support. Capix is also the sole partner for Cruse high-end scanning equipment.
Products
Services
Ads
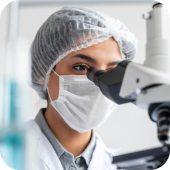
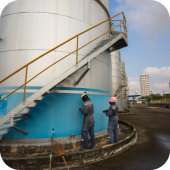
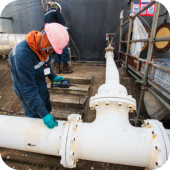