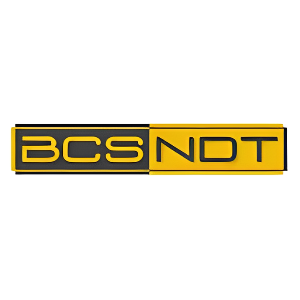
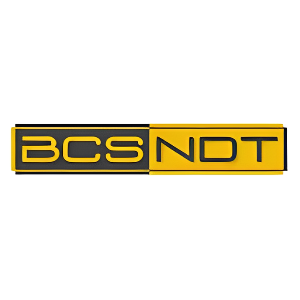
BCS NDT
BCS NDT was created in 2016 in Italy and operates in the Non-Destructive Testing field for the Oil&Gas and Energy sectors worldwide. The company offers welding and NDT engineering support, NDT consultancy, NDT services and training.


Overview
BCS NDT is an Italian company established in 2016 performing non-destructive testing (NDT) worldwide, onshore and offshore, with offices in Italy, Kazakhstan and South Korea. BCS NDT operates in Oil and gas, manufacturing and mining sectors using conventional and advanced NDT methods. The variety of NDT testing ranges from advanced techniques to conventional techniques such as:
Manual Ultrasonic Testing (MUT), Magnetic Particle Testing (MT), Dye Penetrant Testing (PT), Visual Testing (VT). Advanced methods are Phased Array Ultrasonic Testing (PAUT), Automated Ultrasonic Testing (AUT), Time of Flight Diffraction (TOFD) and Eddy Current Array (ECA). BCS NDT has an extensive track record in inspecting onshore and offshore pipelines and piping systems (spool, risers, jumpers) with advanced NDE techniques, forged items, and structures. Materials inspected spread from carbon steel to different types of corrosion-resistant alloys (CRA).
Products
Services
Ads
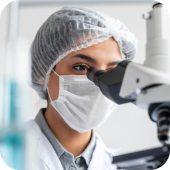
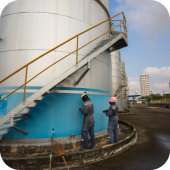
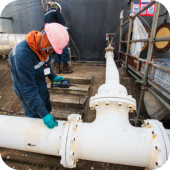