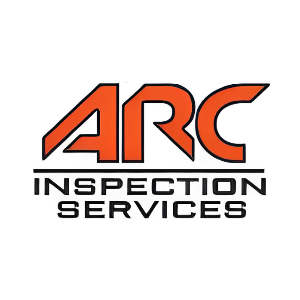
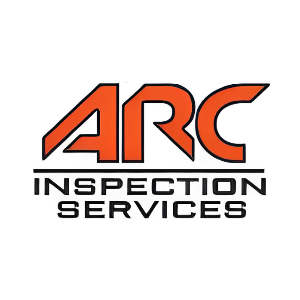
ARC Inspection Services, LLC
ARC Inspection Services, LLC, provides Non-Destructive Examination, Welder Testing services and 3rd Party Inspectors for the pipeline and heavy industrial market.


Overview
ARC Inspection Services, LLC specializes in offering Non-Destructive Examination, Welder Testing services, and 3rd Party Inspection services tailored to the pipeline and heavy industrial sectors.
With a wealth of experience in the Oil and gas, Chemical, and Power industries, ARC Inspection Services, LLC collaborates closely with clients to ensure the integrity of critical pipelines, piping components, process systems, and fabrications. Their goal is to facilitate safe, sustainable operations for their clients.
At the core of ARC Inspection Services, LLC's mission is a steadfast commitment to delivering exceptional customer value. Their approach is rooted in safety, integrity, quality, and productivity. They prioritize these principles in every project, ensuring that their clients receive the highest standard of service.
Driven by a strong motivation to excel, ARC Inspection Services, LLC aspires to be the leading choice in the industrial market for Inspection and Asset Integrity services. They aim to consistently deliver excellence and innovation, setting the bar for quality within their field.
Products
Services
Ads
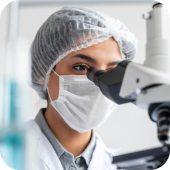
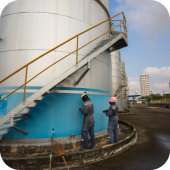
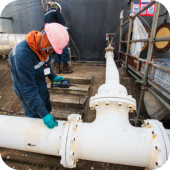