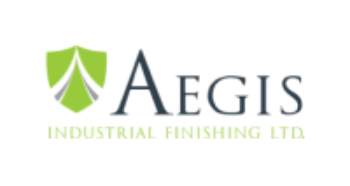
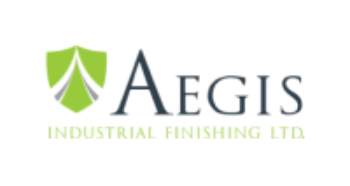
Aegis Industrial Finishing
Aegis Industrial Finishing Ltd. was opened in 2010 to provide the market with the best service, quality, and technical excellence possible by a custom powder coating company.


Overview
Aegis Industrial Finishing Ltd. was opened in 2010 to provide the market with the best service, quality, and technical excellence possible by a custom powder coating company.
With Powder Coating and Sandblasting under one roof, we provide timely and highly customized metal preparation and coating services to your company.
Products
Services
Ads
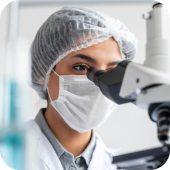
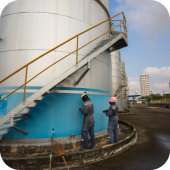
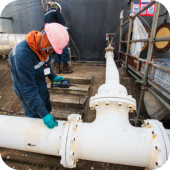