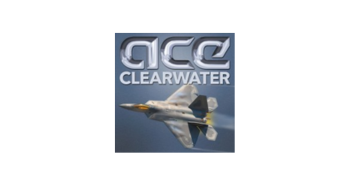
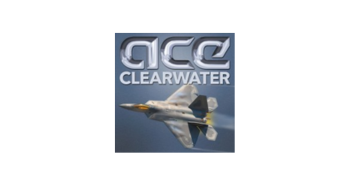
ACE Clearwater Enterprises
Ace Clearwater custom manufactures complex metal forms, components and welded assemblies for the Aerospace and Power Generation industries.


Overview
19815 MAGELLAN DRIVE ::: TORRANCE, CA 90502 ::: 310 538 5380
Ace Clearwater custom manufactures complex metal forms, components, and welded assemblies for the Aerospace and Power Generation industries. Our employees operate from three facilities that combine more than 700,000 sq. ft. within a 10 sq. mile radius in Southern California — Our people stand out as the best problem-solving team in the business. Founded in 1949, ACE continues our long history of dedication to continuous improvement in all areas of Engineering, Forming, Bending, Welding, Machining, Waterjet, and Assembly. Our certifications include ISO 9001:2008, AS9100C, NADCAP Accredited N.D.T., and Welding MIL-I 45208A
Products
Services
Ads
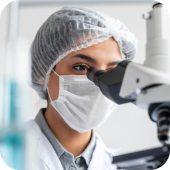
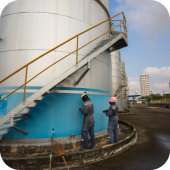
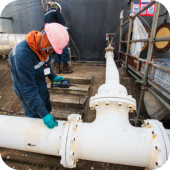