The right tools, appropriate systems and accurate data could make a considerable impact on the ease and speed at which equipment is repaired in your organisation. Verdantix’s latest research suggests that the Covid-19 pandemic is driving organisations worldwide to:
- Invest more in technologies that enable remote operations to ensure business continuity, and
- Those mobile applications are seen as an effective form of digital innovation.
We are currently in the adoption phase of these technologies, which means that there are still plenty of opportunities to improve such products. It is easy to get over-excited about the functions and convenience that mobile technologies promise. Convenience should, however, be seen for what it is; a product characteristic that makes adoption by employees more enticing, while product features would be rendered useless unless the data generated can be shared among applicable enterprise systems.
“Mobile technology doesn’t sit in isolation. The intent behind it is to get information in and out of core systems to enable staff, clients, and everybody who needs to collaborate on a task,” says Stefan Swanepoel, the On Key EAMS Product Manager.
Marthinus Burger, “Pragma’s Head of Projects and Consulting is an asset management specialist with more than 15 ‘years’ experience in CMMS and EAMS implementations, looks at it from a more practical perspective. “While it is all about the apps, it is not just all about the apps. To get the maximum value from mobile applications, you have to ensure that the Work Management and Control process is efficient and that the apps you deploy guides people to provide the right information throughout the process.”
As an engineering firm that has seen clients reap the benefits of improved data velocity and accuracy many times over, Pragma continuously invests in improving our suite of products. Our latest range of apps can significantly improve work identification and feedback on the equipment that needs maintenance or repairs. Our apps can integrate with On Key EAMS, with other systems of record and with each other. Why is this significant? It gives users access to a consolidated set of information and enables them to deliver work more efficiently. While a user might only use one app, they might be interacting with multiple systems on the back-end without realising it. It simplifies the experience and makes it a lot easier to use.
To understand the advantages of mobile technology for logging requests, let’s look at the common challenges of traditional work order systems.
Challenge | Details |
Inconvenient logging processes | Often employees find it inconvenient to log issues or breakdowns because they don’t know where to find the necessary templates, or sending an email becomes a hassle, or the issue has been forgotten by the time they return to their computers. |
Ineffective paper-based systems | This leads to low data velocity, data capturing errors and information getting lost. Because of a lack of guidance, a person might specify the wrong equipment for maintenance, leading to incorrect planning and the actual issue not getting resolved in time. |
No visibility on my current and previous requests | A lack of feedback on work could discourage employees from logging future work requests or lead to duplicate requests from the same or multiple people on the same piece of equipment. |
Duplicate requests | When the validation and verification of requests aren’t done correctly, logging multiple requests on the same equipment can easily occur. This could mean that the planning and scheduling team either duplicates work plans or cancels requests thinking that someone else has already planned for it. |
Work requests not clearly described | Often, and especially with people without a background in maintenance, work requests get logged with incomplete and unstructured information, slowing down the entire process. In turn, automating and expediting work becomes even more complex. |
Difficulty gathering feedback or confirmation of work done | Outdated systems can make it difficult for the person who logged a call to add further information after submitting their request. The planning team might also find it difficult to get hold of the right person to ask for additional information. This can be especially true in a facilities environment, where the person who logged the call is not part of the maintenance team. |
Position in the Work Order Cycle | Work Identification, Validation and Feedback on Work
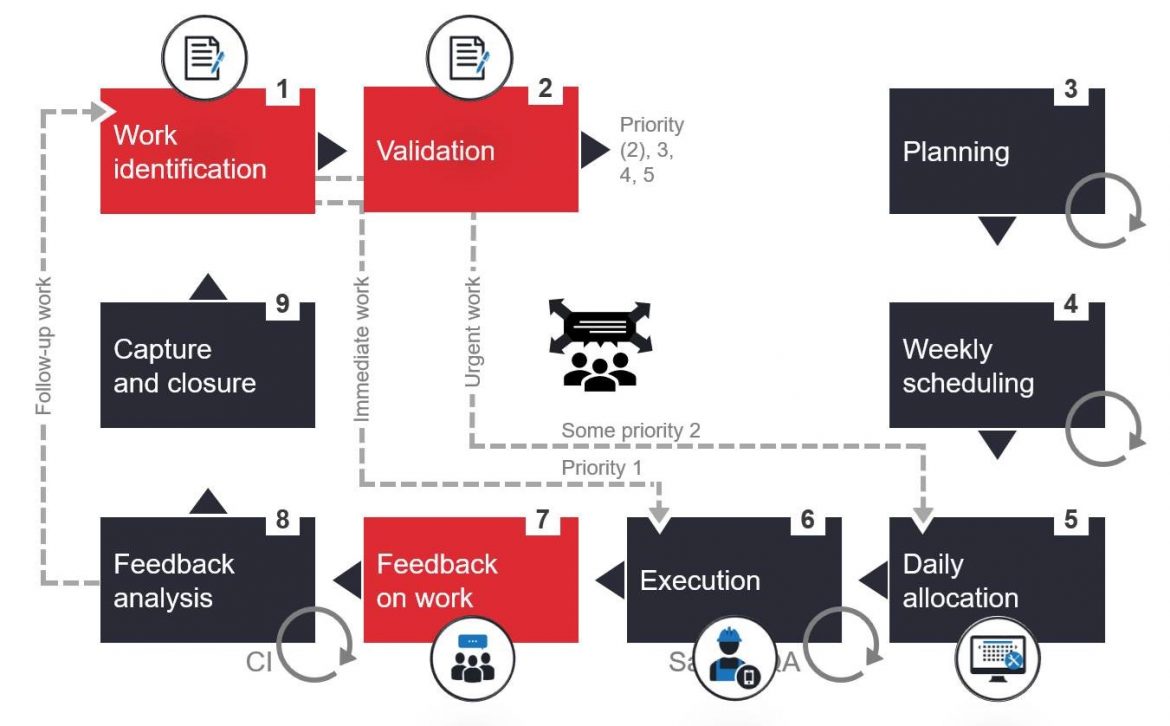
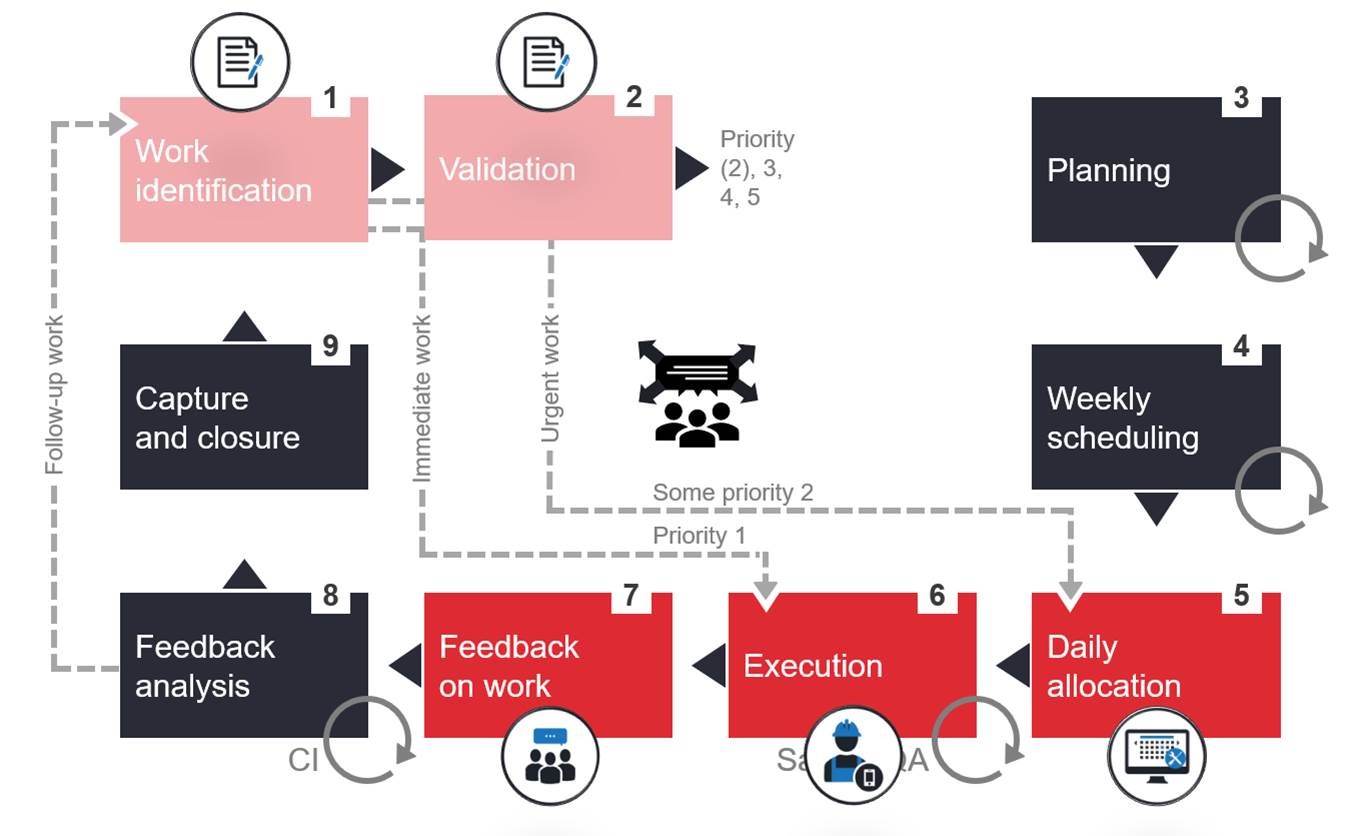