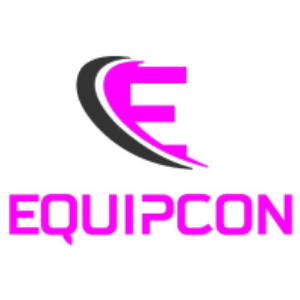
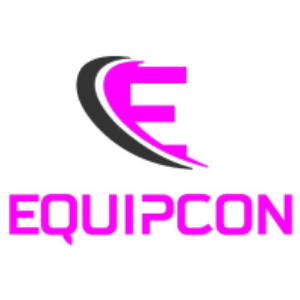
Equipcon Group
CONNECTING EQUIPMENT MANUFACTURERS WITH THE NONDESTRUCTIVE TESTING INDUSTRY.


Overview
With over 30 years serving the NDT and industrial automation markets, Equipcon Group is a leading manufacturer's representative and master distributor with exclusive partnerships currently including ChiNDT and Structural Diagnostics Inc.
We also assist innovators with strategies, sales channel development and management as well as go to market positioning. Maintaining a customs bonded warehouse in the Midwest, we have the capabilities to fully manage your back office and logistics functions.
Along with our growing representative network, we are excited to help revolutionize NDT with features, innovations and unparalleled service and support throughout the Americas.
Products
Services
Ads
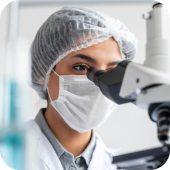
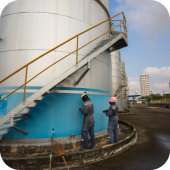
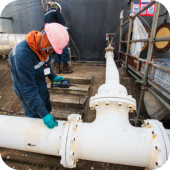