Eddy Current NDT
Tapping into a Hot Solution with ACFM® for High Temperature Inspections
Published on 23rd November 2020
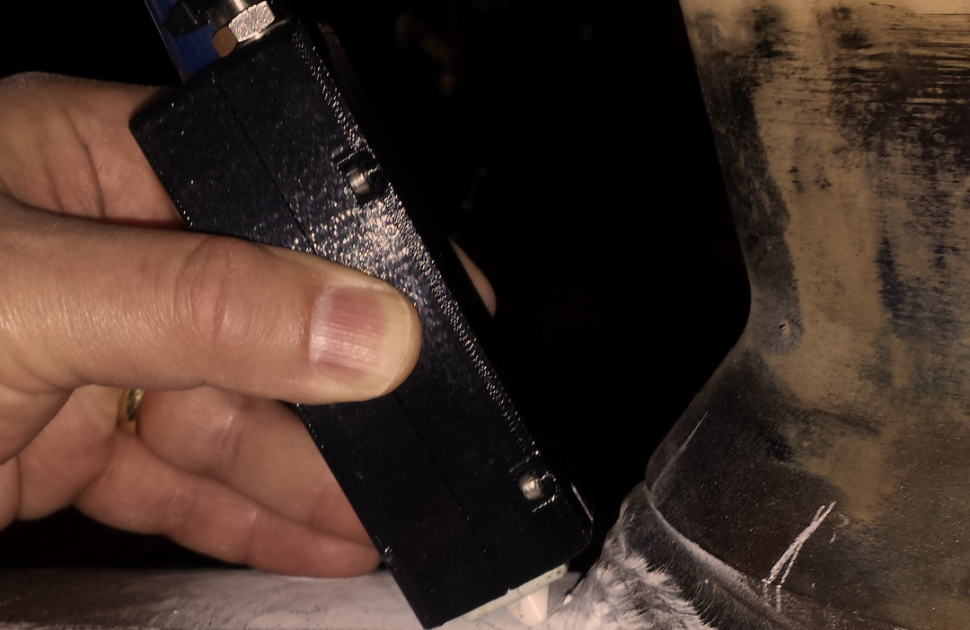
Source:Tapping into a Hot Solution with ACFM® for High Temperature Inspections (eddyfi.com)
Nozzles are typically installed on assets during a turnaround, but an alternative solution offers the advantage of avoiding a costly shutdown. Hot tapping, or pressure tapping, is a specialized process that facilitates safely making a connection to existing pipework or vessels while they remain in service. Hot taps are used for quality control testing; adding temperature or pressure sensors; installing ports, valves, cross-sections, and other piping; removing pressurized casing fluids; and is the initial action taken when a line plug must be inserted.
Hot tapping is only considered when there is no practical alternative as it presents special health and metallurgical concerns for sour gas lines and requires highly trained and experienced crews. Welding on in-service pipelines calls for weld procedure development and qualification. It is critical to ensure the integrity of these welds when pipelines are operating at full pressure and under full flow conditions.
The Challenge
Inspect resultant welds of several hot taps for surface defects 5 millimeters long by 1 millimeter deep (0.2 inches by 0.04 inches) and greater on live gas line operating at 280 degrees Celsius (536 degrees Fahrenheit).
There are three components necessary to safely drill into pipework: the fitting, valve, and hot tap machine. A live gas line required several hot taps. The fittings, in this case Weldolets and a split tee, were attached to the pipe mainly by welding. Consequently, the new welds needed to be inspected for surface breaking cracks with a target defect size of 5 millimeters long by 1 millimeter deep, or 0.2 inches by 0.04 inches. The challenge here was that the pipeline was operating at 280° Celsius, or 536° Fahrenheit.
Conventional inspection methods are restricted at high temperatures. With Magnetic Particle Testing, or MT, the recommended maximum surface temperature using wet fluorescent MT, or WFMT, is 50° to 60° C, or 120° to 140° F. It is limited to water or an oil-based medium for magnetic particles. Some dry powders will work up to 216° C or 420° F, but this was not an option here. Dye Penetrant Testing, PT, has a maximum temperature up to 52° C, or 125° F, although special high temperature penetrants can operate up to 200° C or 390° F. Again, this was not applicable in this case.
The Solution
Alternating Current Field Measurement probe range designed specifically for high temperature environments paired with advanced test instrument.
The Alternating Current Field Measurement, or ACFM®, electromagnetic testing technique has been successfully deployed for high temperature inspections including, but not limited to, hot pipework in petrochemical facilities; defect prone sites under lagging via permanently installed high temperature array probes; and interpass inspection during the welding process without the need for each bead to cool down and be reheated. Standard ACFM probes are rated to 80° C, or 176° F, surface temperature and when special temperature resistant components are used, ACFM probes can inspect in environments 500° C, or 930° F, or more for long periods. The key is the usage of compressed air cooling to the probe while allows for operation at these elevated temperatures. The adhesive used in standard ACFM probes breaks down above 80° C, or 176° F, so a ceramic paste is used in the high temperature probes which has an insulating effect. For the same reason, probe noses are ceramic.
Temperature affects the probe response. Increasing temperatures result in a drop in conductivity and fall in permeability; both affect penetration depth. With the pipeline operating at 280° C, or 536° F, the temperature is far from Curie temperature of approximately 770° C, or 1,390° F, but nevertheless the small reduction in relative permeability can influence test parameters. To establish a phase operational point, a small phase change was required at these temperatures. There is a shift in peak position, or phase, by approximately 10 degrees between the two temperatures. In the following chart, solid lines are ambient while dashed are at 280° C, or 536° F.
In this application, a straight pencil ACFM probe with a micro-nose was chosen due to its small target defect sizing capability. A jacket was created to vortex cool air around the probe and exit around the nose. Compressed air was supplied by a compressor or plant air and delivered to the probe through tubing; a clearance test was performed at ambient temperature.
To validate performance, two samples were created for testing: one 250-millimeter, or 10-inch, pipe with 100mm, or 4in, branch and one 300mm, or 12in, pipe with 250mm, or 10in branch. Each had a range of Electrical Discharge Machining, or EDM, slots cut into the welds. Slot 3 was the target defect size (5mmx1mm/0.2inx0.04in) and slot 1 was below target. The slots shown are the measured values of the slots in the 300mm, or 12in, sample. Slots in the other sample were similar.
Welding pre-heaters were used to raise the temperature of the samples. The temperature was monitored using thermocouples on the pipe and fitting. The maximum temperature used was 300° C, or 572° F. All defects in the samples were detected both above and below the threshold. Contact time was limited to 20 seconds. Procedures were created for effective scanning at elevated temperatures.
The onsite inspection was conducted in two stages. The initial inspection involved scanning a plain pipe at five locations where hot taps were to take place. The probe scanned in a 10mm, or 0.4in, grid pattern both horizontally and in transverse. It inspected the welds after four Weldolets and one split tee were fitted. One indication was identified in the weld cap. It was small but repeatable and measured at 10mm, or 0.4in, long by 0.8mm, or 0.03in, deep. The defect was successfully removed by grinding.
Benefits
- In-service inspection
- No couplant or fluids required
- Huge cost savings
- Accurate measurements of surface breaking cracks that may close when cooled during shutdown
ACFM is an effective technique for surface crack detection at temperatures up to 300° C, or 572° F, in plain pipe and welds without requiring couplant or fluids. Forced air cooling coupled with adjusted nose construction techniques enables sufficient contact times. Pencil probes deployed on carbon steel welds can detect and size defects down to 5mm/0.2in long by 1mm/0.04in deep on real world examples. Additional lab tests have been conducted successfully at 400° C, or 752° F, using the same equipment. Sensitivity will depend on the type of probe used and component material. This superior performance under extreme conditions is an obvious benefit to those responsible for quality assurance in between turnarounds. Besides the significant cost savings by avoiding plant shutdowns, being able to inspect at elevated temperatures avoids the problem of cracks closing when assets are cooled down. ACFM probes and test instruments by Eddyfi Technologies deliver actionable data with ongoing inspection and monitoring throughout an asset’s lifecycle.