Ultrasonic NDT
Robotically Deployed Visual and Ultrasonic Testing for Extended Vertical Pipeline Assessments
Published on 17th July 2020
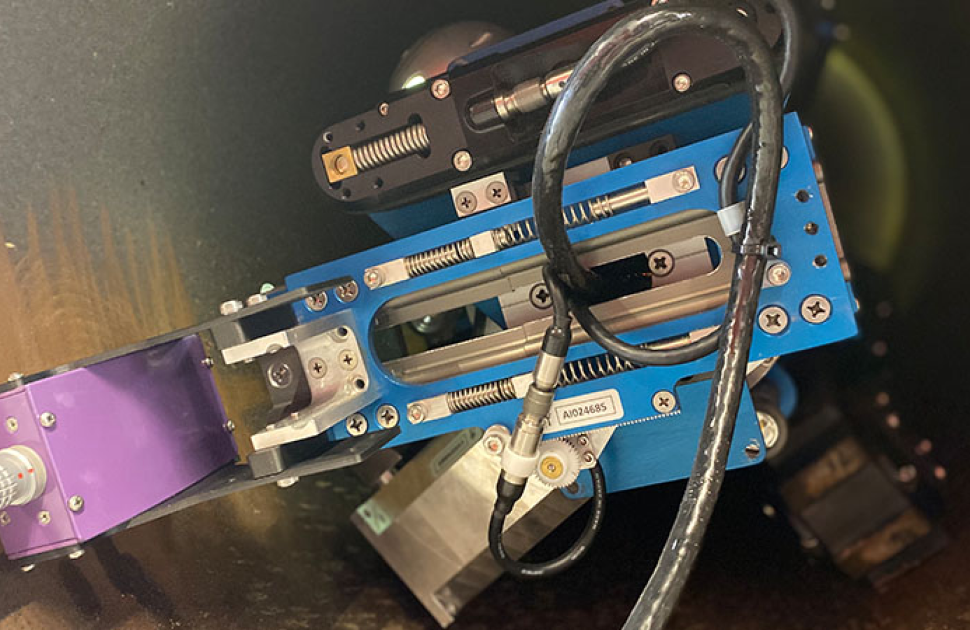
With the introduction of robotics employed for Non-Destructive Testing (NDT) applications, industry has seen a shift towards unmanned inspections to further promote worker wellbeing in environments that are neither physically accessible nor safe for direct human intervention. Industry leaders have set a precedent to completely eliminate Confined Space Entries (CSE) by 2025 and others are following suit.
When it comes to Remote Visual Inspection (RVI) of pipelines, a common request received is for the integration of an Ultrasonic Testing (UT) scanner to measure wall thickness and map corrosion from inside the pipe. Several solutions exist for short distance UT or corrosion mapping, and we offer a number of these already through both our Inuktun and Silverwing brands.
The Challenge
Perform visual inspection and UT thickness measurements of sections of pipe to confirm nominal wall loss with UT scanner positioning controllable by inspector—operating robotic crawler up to 1,000 meters away from entry point inside pipeline containing vertical sections.
Remote visual inspection over limited lengths of piping found in the oil, gas and petrochemical sector or nuclear industry is a common task for inspection robots. The true challenge arises with long range pipeline inspections. A specific requirement to examine vertical pipework presents an additional obstacle. Not only must the robot travel up to one kilometer, it needed to do so vertically without falling. Navigating through a given number of bends or elbows, across mandrel joints, flanges and raised circumferential weld cap is no easy task.
Another consideration is the ability to obtain more than just visual data when closing large sections of pipeline for inspection. Collecting additional UT/EC (Eddy Current) data has become the number one request for long-distance pipeline inspections using robotic crawlers. Unfortunately, the majority of solutions available either cannot incorporate UT/EC, or can only integrate over short distances, i.e. 30 meters (100 feet) or less. As such, solutions have historically been limited to custom solutions with low volume, long turnaround times, high maintenance costs and even higher prices. Eddyfi Technologies looks to change that using this platform to highlight the combination of two brands resulting in a solution that answers a question that has had no answer for some time.
The Solution
Pipe inspection crawler capable of travelling vertical distances up to 1,000 meters in a single run with ability to integrate UT scanner. Robot controller and acquisition device managed as Windows-based applications from a single rackmount interface.
The Inuktun VT150 Vertical Crawler™ (VT150VC) is a robot that uses three equidistant circumferentially engaged tracks, maintaining the central position of the robot within the pipe – the best place for any visual inspection equipment to be mounted offering the best, most unobstructed view when navigating and reducing the effects of halation or exposure compensation. Given its capacity to travel 1,000 meters (3,280 feet), operate in pipelines between 400 and 800 millimeters (16 to 31 inches), manipulate and position a UT probe inside a pipe at several locations to allow for scanning, and operate with limited couplant, the VT150VC met all project prerequisites.
Swift was selected as the acquisition device which connected to the Silverwing R-Scan dry wheel probe and a custom tether. Both robot controller and Swift use a Windows-based operating system and were therefore managed as applications from the rackmount interface used to control the crawler.
Following the initial lab, then field-based trials, it was clear that within a short period, we were able to produce a viable working solution based on strong brand synergies. Our job as technology providers and engineers is to solve the problems of our customers and clients while sometimes overcoming challenges encountered elsewhere.
Silverwing Swift Acquisition Device with B-scan showing pipe thickness along cardinal point over six meters
It is clear that in this transitional period, moving from manned to unmanned inspection, in an age where technology is progressing so fast in all walks of life that we are beginning to uncover new challenges. Our customers are faced with these ever-changing challenges on a daily basis. The future of long-range inspection robotics is subject to the ability to integrate more and more decision-making aids into these hard-to-reach locations.
Eddyfi Technologies is best positioned to work internally to create solutions for new problems because we have a broad and experienced, global team who collaborate to create the best possible solution for your operational needs. We fully understand that the inspection landscape is changing and that the scope is becoming wider and wider. With Eddyfi Technologies, you do not need to worry about the future, as we are already looking to solve the problems of tomorrow today.
Benefits
- By leveraging existing technology, we offer a quicker market solution based on two well-known brands’ years of industry knowledge.
- Further integrations will empower robotic deployment of other NDT sensors in hard-to-reach or hazardous environments.
Inspection robots offer a number of benefits for remote inspection of storage tanks, pressure vessels, and complex pipework. This includes reducing or eradicating the need for scaffolding, rope access, shutdowns, and prior cleaning or extensive preparation. In addition, robotics may be integrated into inspection programs that can accommodate more frequent assessments given the increased cost and production efficiencies gained with these capable systems.
The initial driver to consider this particular project is the fact that Eddyfi Technologies already specializes in RVI and UT. This cross-technology ability enables our specialists to collaborate and produce the best solution for the task. This translates into better consideration for a solution-based approach, product selection complementary to existing technology, reduced requirement for custom parts, in-depth understanding of customer project goals, and lower overheads and therefore reduced client costs.