Ultrasonic NDT
QUALITY CONTROL OF COMPLEX GEOMETRIES
Published on 14th April 2023
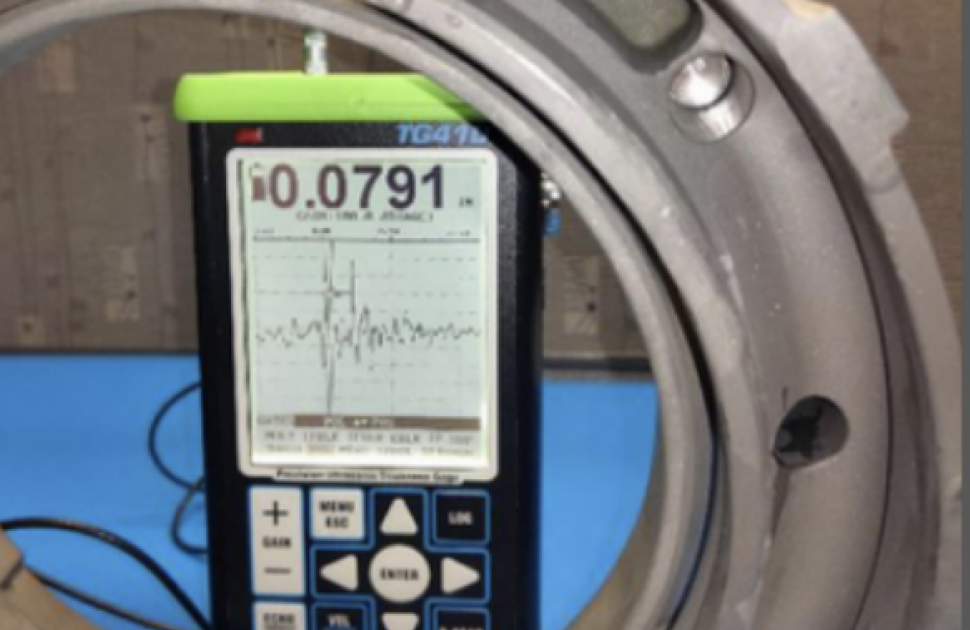
Background
Mission success depends on reliable, high-performance parts. Effective quality
control of manufactured parts is necessary to ensure they perform their
intended function without fail. This is especially true for advanced parts with
complex geometries. One way of verifying conformance to specification is
through-thickness gauging. On complex parts, accurate and repeatable thickness
readings can be difficult to obtain with standard mechanical measurement
methods. More advanced methods, like radiography, are expensive and have
their limitations. For these types of applications, Ultrasonic Thickness Gauging
provides a precise, reliable, and economical solution.
Ultrasonic Thickness Gauging delivers a precise measurement of wall thickness
by sending out a sound wave and “listening” for the return echo. This “pulseecho” method only requires access to one side of a wall, enabling measurement
where one side of the part is obstructed. Probe faces can be small, and attached
to angled handles, allowing measurement within physically restrictive
dimensions. Measurements can also be performed quickly. Once a probe and
gauge are set up for a specific material, contact with the part at different
locations will yield instant and repeatable readings.
Equipment
TG-410 Thickness Gauge
- Single and dual element transducers
- Contact, delay/immersion, through-transmission, shear mode
- High-Speed LCD Display
- Freeze-screen direct access button
- Split-View: Dual A-Trace display
- Split-Scan: View A-Scan and time-encoded B-Scan simultaneously
- Peak Echo Hold: Fixed or timed "waterfall" reset
- Default and user-programmable setups
- Rugged aluminum case with rubber end caps
- Optional Windows-based Data Transfer software
Technical Outline / Procedure
A regular customer of NDT Systems required assistance in improving
their quality control process. They needed to measure the wall
thickness of various regions on the pictured part but were not able to
take reliable readings with other methods they tried. It was
determined to use an NDT Systems TG-410 Thickness Gauge in
conjunction with an AE12205-A ultrasonic probe. The TG-410 is an Atrace capable device with adjustable gain and gates, and the AE12205-
A is a 12MHz pencil-style probe with an angled shaft.
Cast parts are generally acoustically attenuative, and the higher
frequency needed for precise measurements can be difficult to resolve
without a waveform trace and adjustable gates. By setting the gain
high enough on the TG-410, and blocking out the excess noise from the
initial pulse, repeatable measurements down to four decimal places
with an 80% FSH are achievable. The delay line on the AE12205-A
enables higher gain settings than a comparable contact transducer by
delaying the interface echo, allowing the user to determine which
signals are noise and which are valid echoes.
After observing the successful measurement of the part, the
customer decided to purchase the TG-410 and the AE12205-A and
implement them in their production quality control process.
For thicker parts manufactured with more acoustically attenuative
materials, pairing the AE12205-A with the NDT Systems Novascope
6000 Precision Thickness Gauges would be a more robust solution.