Ultrasonic NDT
Portable Ultrasonic Testing Solutions for Rail Inspections
Published on 7th June 2020
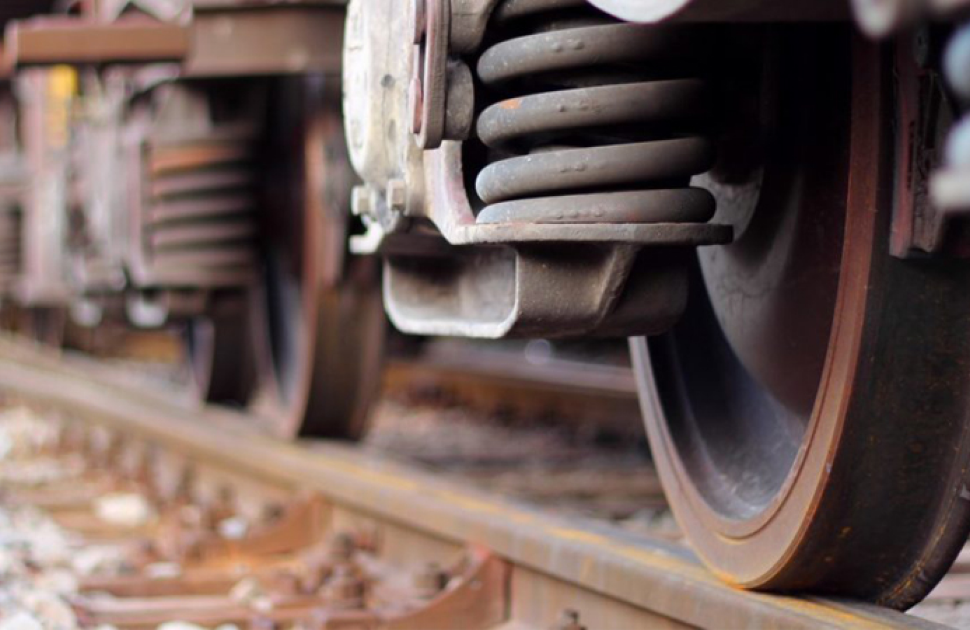
Wear-related deformation and damage, however, tends to fall into a few specific categories:
- Friction: Friction-related wear can occur wherever the train’s rolling wheel flange contacts the rail. Lateral wear presents itself on the gauge face when the rail is on the high side of a curve. Vertical wear forms on the running surface where the wheels and rail interact.
- Plastic flow: The wheel’s small contact patch produces extremely high stresses on the rail, especially in curves. The heat and pressure can cause the metal to deform near the surface and change the rail’s shape. The depth of this plastic flow depends on the hardness of the rail and the severity of the curve.
- Manufacturing defects: The rail manufacturing process can introduce flaws due to residual stress from roller straightening and head hardening.
- Rolling contact fatigue (RCF): Rolling contact fatigue is perhaps the most pervasive cause of rail damage on heavy-haul rail lines. Cracks can appear on the rail surface (e.g. head checks, shelling, squats) or the subsurface and then propagate as a result of contact stresses between a wheel and the rail.
The Latest Generation in Ultrasonics
Ultrasonic testing (UT) is the primary method for detecting and sizing defects through cross-sections of a rail, using a localized immersion system. The latest generation of phased array UT instruments and probes gives technicians a range of methods they can use to conduct inspections in the field quickly. Speed is essential given the amount of track that technicians are required to examine.
UT inspection results are recorded in a digital format, which means technicians can apply different processing algorithms immediately or in the future. And because of advancements in software, portability, and battery life, technicians can bring this computing power virtually anywhere, including on a chase vehicle during a track inspection in a remote area.
There are two UT methods used in rail inspections today:
- Conventional or standard UT: In simple terms, a conventional or standard UT probe is capable of generating and receiving a single ultrasonic beam. The focal point and angle of the beam are fixed, which can make it more difficult to locate and visualize flaws especially in components with complex geometries. Probe frequency is chosen based on the characteristics of the material to inspect.
- Phased-array UT (PA UT): Phased-array UT is an advanced inspection method that uses multiple individual elements (typically from 16 to 64) in a single probe. By exciting each element in a controlled manner, a phased-array UT instrument can produce a precise beam shape and generate two and three-dimensional views of a flaw with greater speed and accuracy.
This is particularly true of rail with severe head wear distortion or other types of plastic flow. Severe deformation can alter the normal angle refraction of the ultrasonic beam to such a level that the signals don’t penetrate the rail at the expected angle or reach the expected location. Therefore, it’s possible that reflected sound beams normally associated with internal rail flaws may not be properly identified. If the head-wear characteristics are significant, it can impact the integrity of the test.
Phased array UT can improve probability of detection (POD) and better characterize potential indications in a broad range of defects, including plastic deformation.
Conclusion
There have been a number of industry developments and guidance to reduce the risk of severe rail wear, including the use of eddy current inspection technology to detect surface defects and RCF-related fatigue. However, UT is an essential nondestructive testing (NDT) method for rail inspections. Well-trained NDT technicians using the right combination of ultrasonic techniques and advanced technology can do their part to keep the rail industry on the right track.
Source: https://www.zetec.com/portable-ultrasonic-testing-solutions-for-rail-inspections/