Ultrasonic NDT
Navigating through complex inspections using simulation software
Published on 23rd September 2020
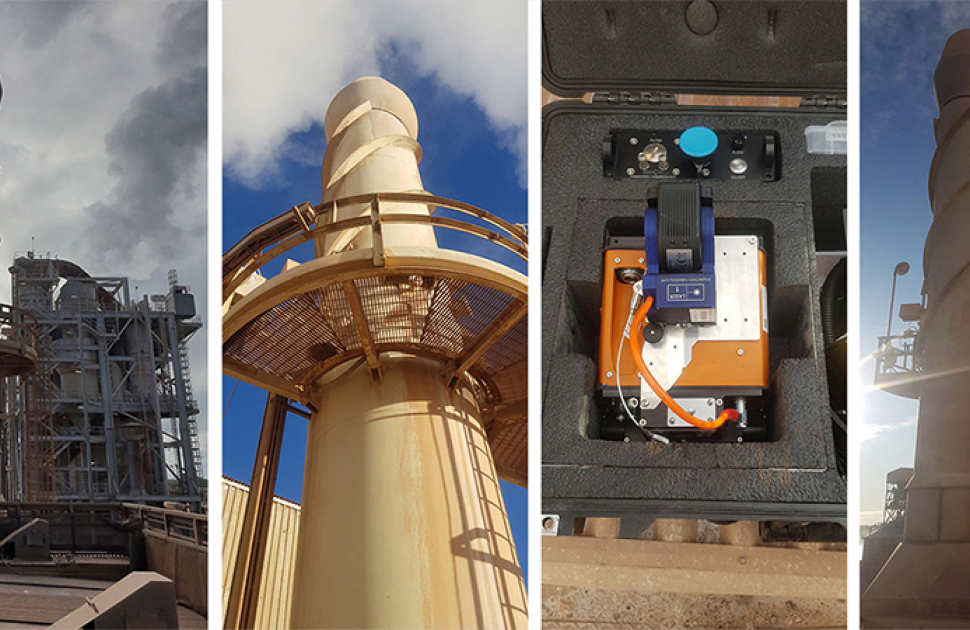
THE CHALLENGE
An operator requested advice and a suitable inspection solution to take thickness readings on one of their vertical stacks. There was only one access point on the 16-metre-high asset, which was a small platform that went halfway around the perimeter.
The stack had three fins that spiral around the outside, to the top of the asset. The readings had to be taken along a path between each of these fins. The material of the stack was carbon steel, with a paint coating, there was no information regarding the condition of the material towards the top of the stack.
EVALUATION AND 3D SIMULATION
To complete this scope, a method of taking thickness readings of carbon steel with a paint coating needed to be done. There also needed to be a way of accessing the entire area of inspection.
Access on the stack was limited, as there was no option for rope access, so the inspection had to be conducted from the ground. The platform only covered one side of the stack, which meant access on the opposite side was limited, this meant there was no line of sight during the inspection.
As there were also fins approximately 250mm wide that extended past the platform, accessing the opposite side of the stack was physically obstructed.
Nexxis’ dedicated Engineering team were able to gather all the relevant data on the asset from the asset owner and input this information into Nexxis’ 3D simulation inspection software, nexSIM.
By using nexSIM, the engineers were able to create a simulation of the inspection and decide the perfect solution for the scope.
The simulation also assisted the service provider in planning and carrying out the inspection using Nexxis’ methodology.
THE SOLUTION
This inspection was performed with the use of a magnetic wheeled crawler, due to the limited access of the asset. The crawler that was selected by Nexxis and used by the service provider was designed to have optimal manoeuvrability on a curved surface while maintaining maximum adhesion. The crawler also carried a payload consisting of a twin crystal ultrasonic probe, couplant supply and signal wire, along with the crawler’s own power and communication cable.
To take the measurements on the far side of the stack, just like in the simulation inspection, the crawler was able to negotiate the geometry of the fins or be placed onto a fin and transition onto the surface of the stack.
CONCLUSION
The crawler was able to successfully drive to the top of each path and take UT readings along the way. As the crawler approached the top, it was found that there was more dirt on the surface, making UT more difficult, in some cases, a crawler can be manually adjusted side to side to attempt to improve the signal.
The adhesion of the crawler was sufficient to hold the entire system during the inspection, however, to reduce the weight the tether was dragged along the fin instead of hanging directly down.
Taking measurements at regular intervals to keep the UT data consistent was possible with onboard encoding from the crawler. The toughest element of the inspection was getting the crawler to drive straight while moving diagonally across a curved surface, due to nexSIM’s pre-inspection software Nexxis’ Engineers were able to work closely with the service provider to familiarise themselves with this challenge. Resulting in a successful inspection that met all the operator’s outcomes and needs.
To learn more about using nexSIM for your next remote visual or NDT inspection contact one of our engineers at nexxis.com.